Am Massachusetts Institute of Technology (MIT) wurden die ersten vollständig digital gefertigten Plasmasensoren entwickelt. Diese auch als Retarding Potential Analyzer (RPA) bezeichneten Messgeräte sind eine Weiterentwicklung des traditionellen Faraday Cups und dienen der Bestimmung von chemischer Zusammensetzung und Ionenenergieverteilung in Plasmen.Die 3D-gedruckten und lasergeschnittenen Bauteile schnitten genauso gut ab wie die weitaus teureren und aufwendiger im Reinraum hergestellten Halbleiter-Plasmasensoren. Im Gegensatz zu diesen können die 3D-gedruckten Sensoren jedoch innerhalb weniger Tage deutlich günstiger gefertigt werden. Aufgrund der geringen Kosten und schnellen Herstellung sind die Sensoren ideal für eine Einsatz auf den kostengünstigen, leichten und stromsparenden CubeSats, die häufig zur Kommunikation und Umweltüberwachung in der oberen Erdatmosphäre betrieben werden.
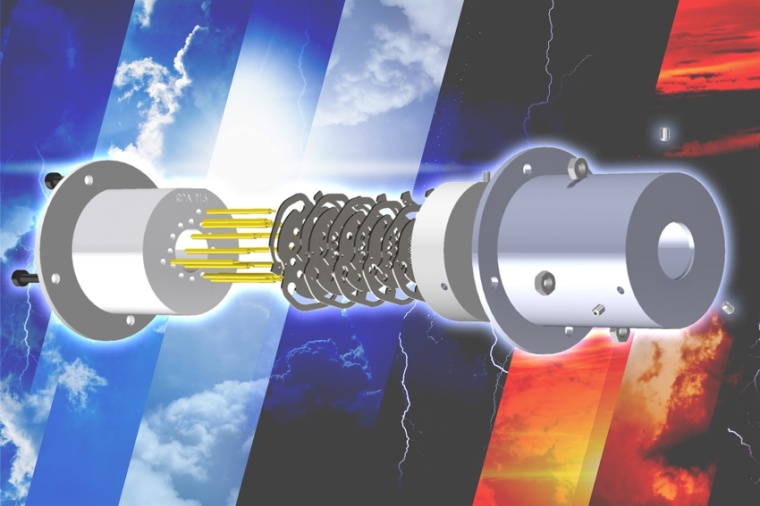
Die RPAs werden unter Verwendung eines glaskeramischen Materials hergestellt, das haltbarer ist als herkömmliche Sensormaterialien wie Silizium und Dünnschichtmaterialien. Durch die Verwendung der Glaskeramik in einem Herstellungsprozess, der für den 3D-Druck mit Kunststoffen entwickelt wurde, konnten die Sensoren mit komplexen Formen hergestellt werden. Sie halten daher den großen Temperaturschwankungen stand, denen ein Raumfahrzeug in der unteren Erdumlaufbahn ausgesetzt ist.
Ein RPA wurde erstmals 1959 bei einer Weltraummission eingesetzt. Die Sensoren erkennen die Energie von Ionen oder geladenen Teilchen in einem Plasma, wie es auch in der oberen Erdatmosphäre vorkommt. An Bord eines Raumfahrzeugs wie dem CubeSat vermessen vielseitigen Instrumente diese Plasmen und unterstützen so Wettervorhersage oder die Überwachung des Klimawandels.
Die Sensoren bestehen aus einer Reihe von elektrisch geladenen Gittern, die selektiv nur die Ionen des zu untersuchenden Plasmas durchlassen. Diese erzeugen einen elektrischen Strom, den der Sensor misst und auswertet.
Entscheidend für den Erfolg eines RPA ist die Gehäusestruktur, die die Gitter ausrichtet. Sie muss elektrisch isolierend sein und gleichzeitig plötzlichen, drastischen Temperaturschwankungen standhalten können. Für die neuen RPS wird ein druckbares, glaskeramisches Material mit genau diesen Eigenschaften verwendet, das Vitrolite.
Vitrolite wurde Anfang des 20. Jahrhunderts entwickelt und häufig für bunte Kacheln verwendet, die in Art-Déco-Gebäuden häufig zu sehen waren. Das haltbare Material kann auch Temperaturen von bis zu 800 Grad Celsius standhalten, ohne kaputt zu gehen, während die in Halbleiter-RPAs verwendeten Polymere bei 400 Grad Celsius zu schmelzen beginnen.
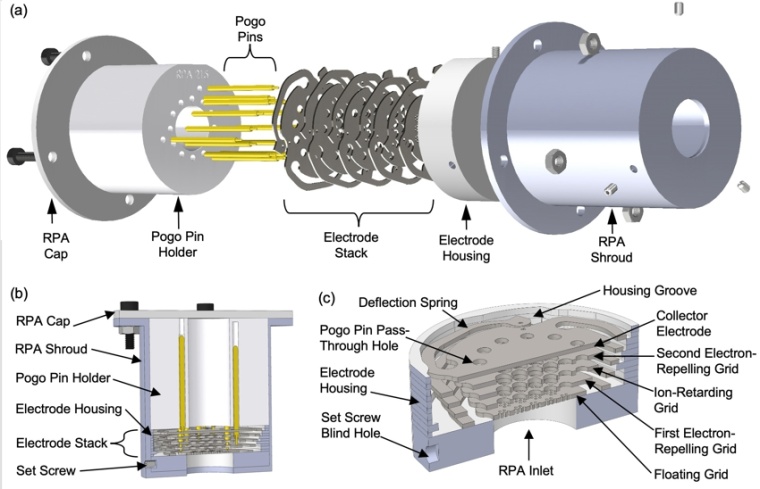
Beim 3D-Druckverfahren für Keramik wird normalerweise Keramikpulver mit einem Laser aufgeschmolzen, um es in Formen zu bringen. Bei diesem Verfahren wird das Material jedoch oft grob und es entstehen Schwachstellen aufgrund der hohen Hitze des Lasers.
Stattdessen verwendete das MIT-Team die Vat-Photopolymerisation, ein Verfahren, das vor Jahrzehnten für die additive Fertigung mit Polymeren oder Harzen eingeführt wurde. Bei der Vat-Photopolymerisation wird eine 3D-Struktur schichtweise aufgebaut, indem sie wiederholt in einen Behälter mit flüssigem Material, in diesem Fall Vitrolite, getaucht wird. Nach jeder Schicht wird das Material mit ultraviolettem Licht ausgehärtet, und dann wird die Plattform erneut in den Bottich getaucht. Jede Schicht ist nur 100 Mikrometer dick, was die Herstellung glatter, porenfreier, komplexer Keramikformen ermöglicht.
In der digitalen Fertigung können die in einer Designdatei beschriebenen Objekte sehr kompliziert sein. Dank dieser Präzision konnten die Forscher lasergeschnittene Netze mit einzigartigen Formen herstellen, so dass die Löcher im RPA-Gehäuse perfekt aufgereiht waren. Dadurch können mehr Ionen durchgelassen werden, was zu höher aufgelösten Messungen führt.
Die preiswerte und schnelle Produktion gestattet die Herstellung vier verschiedener Designs., von denen eines besonders effektiv bei der Erfassung und Messung eines breiten Spektrums von in der Umlaufbahn eine Satelliten vorkommenden Plasmen ist, während ein anderes sich gut für die Erfassung extrem dichter und kalter Plasmen eignete, die normalerweise nur mit hochpräzisen Halbleitergeräten gemessen werden können.
Diese hohe Präzision könnte 3D-gedruckte Sensoren für Anwendungen in der Fusionsenergieforschung oder im Überschallflug ermöglichen. Velásquez-García fügt hinzu, dass das Rapid-Prototyping-Verfahren sogar zu mehr Innovation bei der Konstruktion von Satelliten und Raumfahrzeugen führen könnte.
Obwohl Velásquez-García mit diesen Sensoren bereits zufrieden ist, möchte er in Zukunft den Herstellungsprozess verbessern. Durch eine Verringerung der Schichtdicke oder der Pixelgröße bei der Glaskeramik-Vat-Photopolymerisation könnten komplexe Bauteile entstehen, die noch präziser ist. Darüber hinaus würde die vollständig additive Fertigung der Sensoren deren Kompatibilität mit der Herstellung im Weltraum ermöglichen. Er möchte auch den Einsatz künstlicher Intelligenz erforschen, um das Sensordesign für bestimmte Anwendungsfälle zu optimieren, um beispielsweise ihre Masse stark zu reduzieren und gleichzeitig ihre strukturelle Stabilität zu gewährleisten.
MIT / LK
Weitere Infos