3D-Druck für Raketentriebwerke
Fertigungsverfahren für schnell rotierende Bauteile im Test.
Im Projekt SeLEC – Selective Laser Melting – von Komponenten für Raketentriebwerke haben Wissenschaftler des Instituts für Werkstoff-Forschung und des Instituts für Raumfahrtantriebe des Deutschen Zentrums für Luft- und Raumfahrtein schnell rotierendes, im metallischen 3D-Druck gefertigtes Pumpenbauteil für Flüssigkeitsraketentriebwerke erfolgreich entwickelt und getestet. Die Turbomaschinen sind unabdingbare Komponenten für ein effizientes Flüssigkeitstriebwerk. Sie fördern den Treibstoff und erzeugen einen hohen Brennkammerdruck – beides wird durch ein schnell rotierendes Pumpenlaufrad, den Impeller, erreicht.
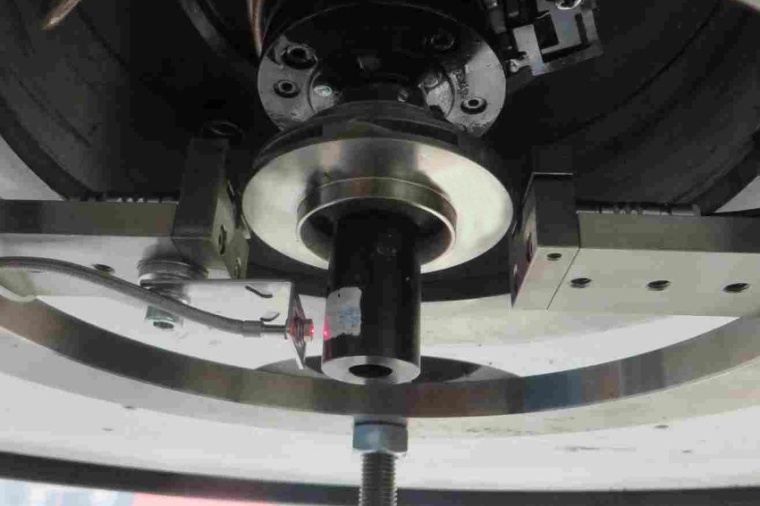
„Ziel dieser Kooperation war es, die Auslegung der Bauteilgeometrie eines Impellers mit einem zukunftsweisenden Fertigungsverfahren zu realisieren“, erklärte DLR-Forscher Wolfgang Kitsche. Der Pumpenimpeller, als Hauptkomponente im Treibstofffördersystem eines Raketentriebwerks, muss dabei den Anforderungen eines späteren Flüssigkeitstriebwerks für Raketenoberstufen gerecht werden. Dabei untersuchten die Wissenschaftler, wie sich dynamische Kräfte auf das gedruckte Bauteil auswirken, wie sich Titanlegierungen als Werkstoff bei dieser Verwendung bewährt und ob der additive Herstellungsprozess für schnell rotierende Bauteile geeignet ist.
Mit diesem zukunftsweisenden Fertigungsverfahren können schnell rotierende hochbelastete Bauteile in einem Stück und ohne innere Stützstrukturen hergestellt werden. „Im Rahmen von SeLEC haben wir eine komplette Fertigungskette mit einer speziellen Baustrategie entwickelt, um die inneren Kanäle des Impellers ohne Stützstrukturen zu drucken“, erläuterte Guillermo Requena, Abteilungsleiter Metallische Strukturen und Hybride Werkstoffsysteme, vom DLR-Institut für Werkstoff-Forschung. „Diese Erkenntnisse, insbesondere das Drucken ohne innere Stützstrukturen, sind sehr wertvoll für die Weiterentwicklung diverser anderer Bauteile im 3D-Metalldruck.“
Metallische 3D-Druckverfahren wie das Selektive Laserschmelzen (SLM) gehören zu den additiven Verfahren und bieten gegenüber den konventionellen Fertigungsverfahren und der herkömmlichen Bauweise gleich mehrere Vorteile für das Design des Impellers. So kann dieser gedruckt aus einem Stück bestehen und besitzt somit nicht die typischen Schwachstellen, die ein aus mehreren Komponenten zusammen gelötetes oder geschweißtes Bauteil aufweisen würde. Auch erhoffen sich die Forscher, mit dem metallischen Drucken neue Geometrien von Bauteilen umsetzen zu können, die langfristig die Konstruktion eines kosten- und leistungseffizienteren Triebwerks ermöglichen.
Der 3D-Druck im Pulverbett mit dem SLM-Verfahren ermöglicht herausragende Vorteile bei der Fertigung von Bauteilen mit inneren Kanälen und Hohlräumen. Der mit einer Deckscheibe geschlossene Pumpenimpeller mit seinen inneren Strömungskanälen war daher ein ideales Entwicklungsobjekt für diese Fertigungsverfahren. Die besondere Herausforderung war in diesem Fall das Drucken des Bauteils ohne innere Stützstrukturen, die normalerweise unumgänglich sind, um Bereiche wie die Deckflächen der inneren Hohlräume auf dem Pulver aufzubauen. Hierzu wurden verschiedene Fertigungsstrategien mit unterschiedlichen Bauorientierungen und Stützstrukturstrategien, einem geeigneten Post-Processing sowie die resultierenden Materialeigenschaften untersucht.
Als Werkstoff wurde bei der Fertigung die Legierung Titan-6-Aluminium-4-Vanadium gewählt, die die Anforderungen an dieses rotierende Bauteil sehr gut erfüllt. Das Vanadium bietet im Verhältnis zum Gewicht eine hohe Festigkeit, und es können hohe Drehzahlen im Verhältnis zur Baugröße erreicht werden. Die Erfahrung mit 3D-gedrucktem Titan sind in der Pumpentechnologie noch nicht weit verbreitet und konnten in diesem Projekt erfolgreich ausgebaut werden.
Im Auftrag des DLR führte die Firma Schenck-RoTec in Darmstadt Unwuchtmessungen und Schleuderversuche mit 3D-gedruckten Impellern durch, bei denen während des Testlaufs Deformationsmessungen an den Bauteilen möglich waren. Mittels dieser Schleudertests wurden sowohl die komplexe Bauteilgeometrie als auch das Fertigungsverfahren des Impellers qualifiziert. Für die vorangegangene Strukturanalyse wurden die Werkstoffparameter durch uniaxiale Vorversuche ermittelt. Sie ließ eine Bruchdrehzahl von 160.000 Umdrehungen pro Minute erwarten. Nachdem das Bauteil mehrfach oberhalb dieser Drehzahl geschleudert wurde, kamen die Wissenschaftler zu dem Fazit, dass mit SLM gedrucktes Titan-6-Aluminium-4-Vanadium sehr gut für solche schnell rotierenden Bauteile geeignet ist.
DLR / JOL