Elektromotoren specken ab
Neues Kühlkonzept erlaubt den Einsatz von Kunststoffen als Gehäusematerial.
Sollen Elektroautos leichter werden, könnte etwa der Motor aus faserverstärkten Kunststoffen hergestellt werden. Forscher des Fraunhofer-Instituts für Chemische Technologie ICT in Pfinztal entwickeln gemeinsam mit dem Karlsruher Institut für Technologie KIT ein neues Kühlkonzept, das den Einsatz von Kunststoffen als Gehäusematerial ermöglicht. Ein weiterer Vorteil des Konzepts: Die Leistungsdichte und Effizienz des Antriebs werden gegenüber dem Stand der Technik deutlich erhöht.
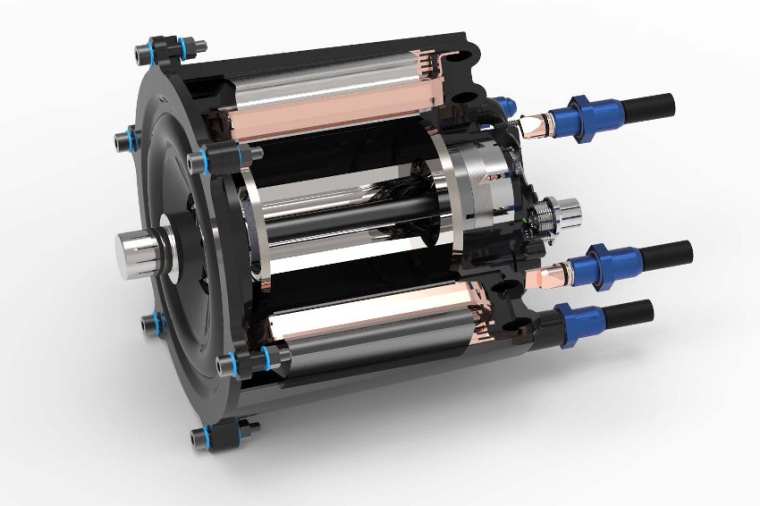
Elektromotor und Batterie bilden die zentralen Elemente des elektrischen Antriebsstrangs. Eine hohe Leistungsdichte, ein geringer Bauraum innerhalb des Elektrofahrzeugs und ein hoher Wirkungsgrad spielen eine besondere Rolle, um eine nachhaltige Mobilität zu gewährleisten. Im Kooperationsprojekt DEmiL, kurz für „Direktgekühlter Elektromotor mit integralem Leichtbaugehäuse“, entwickeln die Forscher ein Konzept, das sich durch die direkte Kühlung von Stator und Rotor auszeichnet. „Ein Elektromotor besteht aus einem sich drehenden Rotor und einem feststehenden Stator. Im Stator befinden sich gewickelte Kupferdrähte, durch die Strom fließt. Hier entsteht ein Großteil der elektrischen Verluste. Die eigentliche Innovation unseres Konzepts liegt im Stator“, sagt Fraunhofer-Forscher Robert Maertens.
Elektromotoren haben einen hohen Wirkungsgrad von über neunzig Prozent. Somit wird ein hoher Teil der elektrischen in mechanische Leistung umgesetzt. Die verbleibenden etwa zehn Prozent der elektrischen Leistung fallen als Verlust in Form von Wärme an. Um eine Überhitzung des Motors zu vermeiden, wird die Wärme im Stator bislang durch ein metallisches Gehäuse zu einem Kühlmantel mit kaltem Wasser abgeleitet. Die Forscherteams ersetzen den Runddraht durch rechteckigen Flachdraht, den man enger auf den Stator wickeln kann. Dadurch entsteht mehr Raum für den angrenzenden, neben den Flachdrähten liegenden Kühlkanal. „Die Verlustwärme kann durch diese Optimierung durch den innenliegenden Kühlkanal abgeführt werden und muss nicht mehr durch das Metallgehäuse nach außen zu einem Kühlmantel transportiert werden. Der Kühlmantel ist in diesem Konzept nicht mehr erforderlich. In der weiteren Konsequenz fällt die thermische Trägheit geringer aus, und zusätzlich erreicht der Motor eine höhere Dauerleistung“, erläutert der Forscher. Darüber hinaus lässt sich durch eine Kühlung des Rotors dessen Verlustwärme ebenfalls im Motor abführen.
Da die Wärme dort abgeleitet wird, wo sie entsteht, können die Projektpartner den kompletten Motor und das Gehäuse in Kunststoffbauweise ausführen und damit weitere Vorteile realisieren. „Kunststoffe sind leicht und sie lassen sich einfacher fertigen als Aluminiumgehäuse. Auch komplexe Geometrien sind ohne Nachbearbeitung möglich, sodass wir in Summe einiges an Gewicht und Kosten einsparen“, so Maertens. Das bisher erforderliche Metall, das als Wärmeleiter diente, kann durch Kunststoff – einen schlechten Wärmeleiter – ersetzt werden. Die Projektpartner setzen auf faserverstärkte, duromere Kunststoffe, die sich durch eine hohe Temperaturbeständigkeit sowie eine hohe Beständigkeit gegenüber den aggressiven Kühlmitteln auszeichnen. Anders als Thermoplaste quellen sie nicht auf, wenn sie mit Chemikalien in Berührung kommen.
Das Kunststoffgehäuse wird im automatisierbaren Spritzgießverfahren hergestellt. Die Prototypen werden in einer Zykluszeit von vier Minuten gefertigt. Die Statoren selbst werden im Transfer-Molding-Verfahren mit einer wärmeleitfähigen Epoxidharz-Formmasse umspritzt. Das Forscherteam hat den Elektromotor hinsichtlich seiner Konstruktion und der Herstellungsprozesse so ausgelegt, dass er sich in Großserie produzieren lässt. Der Statoraufbau ist abgeschlossen, das Kühlkonzept wurde experimentell validiert. „Wir haben in die Kupferwicklungen durch Strom die Wärmemenge eingebracht, die gemäß der Simulation im Realbetrieb anfallen wird. Wir konnten zeigen, dass wir bereits in der Lage sind, mehr als achtzig Prozent der erwarteten Verlustleistung herauszukühlen. Auch für die verbleibenden knapp zwanzig Prozent gibt es schon Ansätze, beispielsweise durch eine Optimierung der Kühlwasserströmung. Aktuell werden die Rotoren aufgebaut, sodass wir den Motor in Kürze auf dem Prüfstand des Elektrotechnischen Instituts betreiben und im Realbetrieb validieren können“, fasst Maertens den Stand des Projekts zusammen.
FhG / JOL