Metallischer 3D-Druck für den industriellen Einsatz
Fraunhofer-Leitprojekt futureAM erreichte bis zum Projektende zahlreiche Technologiesprünge.
Eine Beschleunigung der additiven Fertigung von Metallbauteilen mindestens um den Faktor 10 – mit diesem Ziel startete 2017 das Fraunhofer-Leitprojekt „futureAM – Next Generation Additive Manufacturing“. Sechs Fraunhofer-Institute erreichten jetzt zum Projektende gemeinsam Technologiesprünge in der Systemtechnik, bei den Werkstoffen, in der Prozessführung und bei der durchgängigen Digitalisierung. Sie steigerten so Leistungsfähigkeit und Wirtschaftlichkeit des Metal Additive Manufacturing entlang der gesamten Prozesskette.
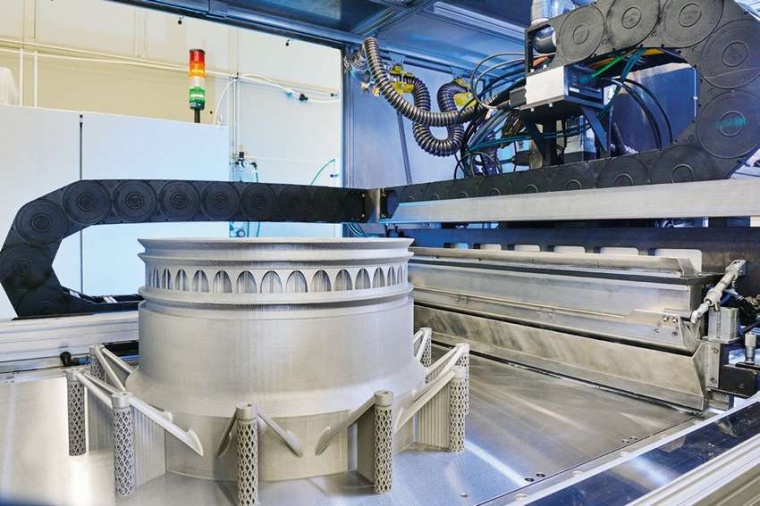
Im Mittelpunkt der Aktivitäten von futureAM steht zum einen die ganzheitliche Sicht auf die digitale und physische Wertschöpfung vom Auftragseingang bis zum fertigen metallischen 3D-Druck-Bauteil, zum anderen der Sprung in eine neue Technologie-Generation der additiven Fertigung. Eine wichtige Rolle spielt dabei das Virtual Lab, welches Kompetenzen digital bündelt und den gesamten AM-Prozess für alle beteiligten Partner transparent macht. „Wir stehen jetzt an der Schwelle zur industriellen Umsetzung“, sagt Christian Tenbrock, Gruppenleiter am Fraunhofer-Institut für Lasertechnik und futureAM-Projektleiter. „Die gemeinschaftlich gewonnene Expertise soll nun in die industrielle Anwendung überführt werden.“
Eine große Herausforderung bei futureAM war das institutsübergreifende Zusammenspiel aller Teilnehmer, die teilweise sehr unterschiedliche Bereiche der gesamten Prozesskette abdecken. Bewährt hat sich dabei das Virtual Lab, das als digitale Plattform den Austausch über alle AM-Aufgabenfelder und -Akteure sicherstellt. In diesem Kontext hat die Fraunhofer-Einrichtung für additive Produktionstechnologien beispielsweise verschiedenste Softwaretools zur Auslegung von AM-Bauteilen entwickelt. Auf diese Weise entstehen webbasierte Simulations-Tools für Metall-AM, mit denen auch Einsteiger arbeiten können.
Im Handlungsfeld Werkstoffe erforschte das Fraunhofer-Institut für Werkstoff- und Strahltechnik, welche Materialien sich in einem Bauteil miteinander kombinieren lassen und welche Probleme dabei auftreten. Unter anderem behandelten die Forscher die Erweiterung des einsetzbaren Spektrums additiv verarbeitungsfähiger Hochtemperaturwerkstoffe und erforschten, wie diese in einer Multi-Material-Bauweise vereint werden können. Ein spannendes Ergebnis brachte das Zusammenspiel von Laserauftragschweißen und künstlicher Intelligenz: Mit Hilfe KI-gestützter Prozessanalyse lassen sich verschiedenste Einflussfaktoren analysieren und so der Fertigungsprozess optimieren. Wie gut das bereits funktioniert, demonstriert das Fraunhofer-IWS an Multi-Material-Bauteilen aus Nickel und Aluminium. Je nach Bauteilanforderungen nehmen die Forscher wahlweise ein drittes oder viertes Element hinzu, um die Eigenschaften exakt an den jeweiligen Anwendungsfall anzupassen.
Die Wissenschaftler vom Fraunhofer-ILT entwickelten ein Demonstrator-System, das ein Maschinenhersteller gebaut hat. Es ist eine Anlage zum 3D-Druck von Bauteilen im XXL-Maßstab: Per Laser Powder Bed Fusion entstand dank des großen Bauraums ein Demonstrator-Bauteil für zukünftige Triebwerksgenerationen von Rolls-Royce. Möglich wird dies durch ein neues Maschinensystem mit mobilem Optiksystem. Ähnliche Erfolge gab es auch beim extremen Hochgeschwindigkeits-Laserauftragschweißen, mit dem sich nun auch 3D-Bauteile herstellen lassen. Der neu entwickelte Prozess erlaubt extreme Auftragsgeschwindigkeiten bei gleichzeitig hoher Detailauflösung.
Großes Optimierungspotenzial identifizierten die Forscher auch in der Nachbearbeitung. Das Fraunhofer-Institut für Werkzeugmaschinen und Umformtechnik entwickelte daher im Rahmen des Projekts dafür eine automatisierte Lösung. Um das physische Bauteil zunächst zweifelsfrei identifizieren und stets nachverfolgen zu können, wird bei der Fertigung ein Code eingearbeitet und später ausgelesen. Dieser sorgt zudem für einen effizienten und störungsfreien Kopierschutz. Im nächsten Schritt wird die Ist-Geometrie des eingespannten Bauteils von Laserscannern erfasst und durch den Abgleich von Soll- und Ist-Geometrie die optimale Bearbeitungsstrategie abgeleitet. Die Bearbeitung erfolgt anschließend automatisch durch einen Roboter und wird im Prozess durch erneute 3D-Scans verifiziert.
Fh.-ILT / RK
Weitere Infos