Mikrosensoren heben ab
Mikrosystemsensoren beweisen ihre Tauglichkeit bei Flugversuchen.
Um Flugzeuge immer leichter und emissionsärmer zu machen, ist unter anderem eine genaue Kenntnis der im Flug auftretenden Lasten und Drücke und deren Verteilung auf die einzelnen Flugzeugkomponenten erforderlich. Das Verfahren zur Bestimmung der Lasten ist für eine Zertifizierung unabdingbar und erfolgt nach langer und aufwändiger Vorbereitung im Flugversuch. Im Projekt KonTeKst (Konfigurationen und Technologien für das emissions- und lärmarme Kurzstreckenflugzeug) hat das Deutsche Zentrum für Luft und Raumfahrt (DLR) ein Sensorsystem entwickelt, das kostengünstig die Druckverteilung um eine Tragfläche genau messen und so die Lasten im Flug bestimmen kann.
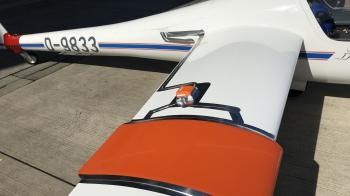
„Beim Design von neuen Flugzeugen werden mittels Simulation verschiedener Belastungsfälle die auftretenden Kräfte und Momente bestimmt und die einzelnen Bauteile entsprechend ausgelegt“, erklärt Christian Raab vom DLR-Institut für Flugsystemtechnik. „Im Flugversuch muss dann nachgewiesen werden, dass die Simulationsmodelle eine hinreichende Genauigkeit aufweisen und die gemessenen Bauteillasten bei ausgewählten Manövern nicht überschritten werden.“ Die Messung der auftretenden Kräfte und Momente erfolgt bisher mit Dehnungsmessstreifen (DMS). Für den Flugversuch mussten die Streifen aufwändig innerhalb von Flügel, Rumpf und Leitwerk aufgeklebt, elektrisch verbunden und kalibriert werden.
Die neue, am DLR-Institut für Aerodynamik und Strömungstechnik entwickelte Messtechnik mit Mikrosystemsensoren (MEMS) kann den Aufwand für die Zulassungsversuche erheblich reduzieren. In Flugversuchen mit dem DLR-Segelflugzeug Discus-2c wurde dieses System erprobt. Der Discus-2c des DLR wird als Referenz für die Ermittlung der Flugleistung von anderen Segelflugzeugmodellen genutzt und ist auch für andere Messaufgaben ausgerüstet. Daher wurden bereits beim Bau innerhalb der Struktur an ausgewählten Stellen Dehnungsmessstreifen integriert. In der Vergangenheit führten die Wissenschaftler am Institut für Flugsystemtechnik bereits eine umfangreiche Kalibration dieser Messstreifen durch, sodass sich an sechs Stationen der Tragfläche Biegemoment, Querkraft und Torsion bestimmen lassen. Dies lässt einen genauen Vergleich der Daten der bisherigen und der neuen Technik zu. Die Daten aus den Flugversuchen werden am Institut für Flugsystemtechnik ausgewertet, um damit vorhandene Simulationsmodelle zu verbessern.
Für die Flugversuche im Projekt KonTeKst integrierten Forscher am DLR die nur fünf Quadratmillimeter großen MEMS-Drucksensoren, die beispielsweise auch in Smartphones oder Tablets eingesetzt werden und weniger als einen Euro pro Stück kosten, in eine biegbare Schaltungsplatine. So entstanden vier Sensorstreifen mit jeweils 16 Drucksensoren. Diese Streifen wurden in einen dünnen Handschuh eingeklebt, der entsprechend mit Bohrungen für die lokale Messung der Drücke versehen wurde. Der Sensorhandschuh kann auf die Tragfläche aufgezogen und nach den Versuchen wieder abgenommen werden, ohne dass Teile an der Struktur verbleiben müssten.
Um die Sensoren auf Herz und Nieren testen zu können, wurden Flugmanöver mit wechselnden Belastungsfällen durchgeführt. Die um das Tragflächenprofil gemessene Druckverteilung wird derzeit im Detail ausgewertet und mit den Ergebnissen der Dehnungsmessstreifen verglichen. „Wir können jetzt nach den ersten Begutachtungen der Daten schon sagen, dass die MEMS-Technik in allen Manövern die gleichen Ergebnisse hervorgebracht hat wie die Dehnungsmessstreifen“, freut sich Raab über den Erfolg.
„Da sich die dabei gewonnenen Erkenntnisse auch auf größere Flugzeugtypen übertragen lassen, haben wir mit dieser Art der Druckmessung eine weniger aufwändige und erheblich günstigere Variante für die Erprobung zukünftiger Leichtbaustrukturen gefunden.“ Das MEMS-Messsystem wird vom DLR-Institut für Aerodynamik und Strömungstechnik nun weiter verbessert, um zukünftige Versuche mit verschiedenen Aufgaben und extremen Umgebungsbedingungen zu ermöglichen. Erste Versuche in einem anderen Höhen- und Geschwindigkeitsbereich sind mit der neuen MEMS-Technik auf dem neuen DLR-Flugversuchsträger iSTAR geplant.
DLR / DE