Sensoren im 3D-Druck
Aktoren und Sensoren lassen sich mit 3D-Druck in komplexe Bauteile integrieren.
Der additiven Fertigung wird eine große Zukunft vorhergesagt. So lassen sich mit Hilfe des 3D-Drucks beispielsweise die Anzahl der Komponenten komplexer, individualisierter Baugruppen stark reduzieren und viele Funktionen direkt in ein Bauteil integrieren. Das vereinfacht den Herstellungsprozess und verringert den notwendigen Bauraum. Um diese Vorteile auch für mechatronische Systeme zu nutzen, forschen Wissenschaftler im Fraunhofer-Institut für Betriebsfestigkeit und Systemzuverlässigkeit LBF in mehreren Projekten an der additiven Fertigung von integrierten Aktoren und Sensoren. Diese können in Leichtbaustrukturen störende oder schädigende Vibrationen mindern sowie Strukturen überwachen.
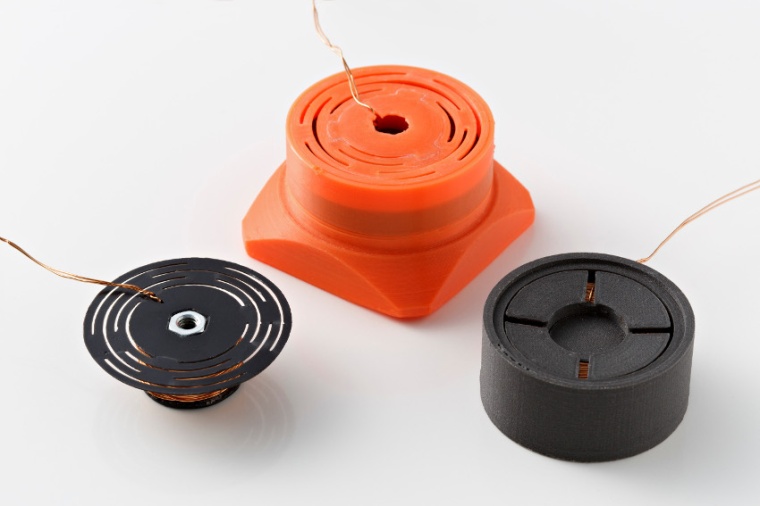
Aufgrund der Ergebnisse ihrer Forschungsprojekte sehen die Wissenschaftler großes Potenzial für die additive Fertigung mechatronischer Systeme: „Additive Fertigung bietet hierfür einen mehrfachen Nutzen. Sensoren können an kritischen Stellen integriert werden, die vorher nicht zugänglich waren: Davon können vor allem leichtbauoptimierte Strukturbauteile profitieren“, erläutert Torsten Bartel, der die verschiedenen Projekte leitete. Zudem lassen sich Aktoren in Kraft und Bauraum so individualisieren, dass keine überdimensionierten Aktoren verwendet werden müssen. Das beschränkt den Materialeinsatz und den Strombedarf auf das Notwendigste. „Schließlich ermöglichen es elektrisch leitfähige Materialien, auf externe Leitungen zur Signalführung und entsprechende Lötarbeiten zur verzichten. So lassen sich kompakte, funktionsintegrierte Systeme mit geringem Montageaufwand herstellen“, sagt Bartel.
Für die additive Herstellung prototypischer mechatronischer Systeme sind gleich mehrere Materialien notwendig, um auf das Einlegen oder Verkleben zugekaufter Aktorik und Sensorik soweit wie möglich verzichten zu können. Besonders eignen sich dafür Fused Filament Fabrication (FFF)-Drucker. Sie sind vergleichsweise günstig und sehr flexibel in der Wahl der zu verarbeitenden Materialien. Mit diesem speziellen Gerät können die Wissenschaftler dank mehrerer unterschiedlicher Druckköpfe in einem Durchgang diverse Kunststoff-Filamente drucken. Neben Standardthermoplasten wie ABS oder PP kommen auch Funktionsmaterialien wie beispielsweise elektrisch leitfähige oder weichmagnetische Materialien sowie Formgedächtnispolymere zum Einsatz. Entwicklungsgegenstand ist es aktuell, mit demselben Drucker elektrisch leitfähige oder auch piezoelektrisch wirksame Pasten zu drucken, die unter UV-Licht ausgehärtet werden. Ziel ist es, eine Vielzahl funktionaler Materialien in der additiven Fertigung zu beherrschen, um vollständig strukturintegrierte Funktionsbauteile umsetzen zu können.
Innerhalb des Projekts Open Adaptronik konstruierten die Darmstädter Forscher einen Tauchspulenaktor, den sie anschließend mit dem FFF-Drucker herstellten. Der Aktor wurde für die mehraxiale Schwingungsminderung an der Kamera eines Quadrokopters ausgelegt. Neben ABS für den Spulenträger mit integrierter Feder nutzten die Wissenschaftler ein ferromagnetisches Filament zur Führung des magnetischen Flusses im Aktorgehäuse. Der notwendige Magnet wurde während des Druckprozesses eingelegt und in das Gehäuse eingedruckt. „Unsere Messungen am fertigen Aktor haben gezeigt, dass sich mit dem additiv hergestellten Aktor vergleichbar große Kräfte erzeugen lassen, wie mit kommerziell erhältlichen Aktoren gleicher Abmessung“, sagt Bartel. Das Material weise zwar eine geringe magnetische Permeabilität auf, aber der Bauraum könne optimaler gestaltet werden.
Darüber hinaus untersuchten die Wissenschaftler die Möglichkeit, mit Hilfe der additiven Fertigung sensorische Funktionen in Bauteile zu integrieren. Ziel war es, den Strukturzustand in autonomen Fluggeräten zu überwachen. Hierfür wurden verschiedene elektrisch leitfähige Kunststofffilamente untersucht und verglichen. Im Anschluss gelang es den Wissenschaftlern, prototypisch Dehnungsmessstreifen und Kraft- bzw. Beschleunigungssensoren im 3D-Druck zu fertigen. Durch neue Materialien mit einer höheren elektrischen Leitfähigkeit wollen die Darmstädter Forscher die Empfindlichkeit der Sensoren in zukünftigen Anwendungen weiter verbessern.
Fh.-LBF / JOL