Alu-Stahl-Hybride effizienter formen
Neues Verfahren verbessert Umformbarkeit von Aluminium-Bauteilen im Karosseriebau.
Bei der Herstellung von Fahrzeugkarossen werden vor allem Materialien verwendet, die möglichst leicht, hochfest, gleichzeitig aber zäh sind. Aluminium, höchstfeste Stähle sowie insbesondere Alu-Stahl-Hybride gelten in diesem Zusammenhang nach wie vor als idealer Kompromiss gewünschter Materialeigenschaften bei guter Kosten-Nutzen-Balance. Eine bereits etablierte Möglichkeit das Gewicht moderner Fahrzeugkarosserien zu senken besteht darin „Tailor Welded Blanks“ einzusetzen. Dies sind Blechplatinen bei denen entsprechend der späteren Beanspruchung Blechzuschnitte mit unterschiedlichen Dicken oder Werkstoffeigenschaften zunächst im flachen Zustand verschweißt und anschließend mittels Umformen und Tiefziehen zu leichtbauoptimierten Bauteilen weiterverarbeitet werden.
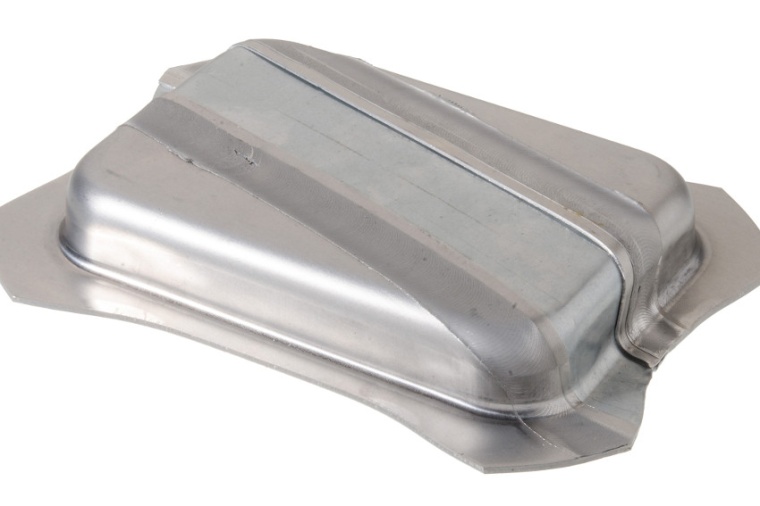
Was bei Stahlplatinen kein Problem ist, kann bei Aluplatinen problematisch werden: Die Schweißnaht hat eine geringere Festigkeit als der umgebende Werkstoff, da Aluminium durch das Schweißen lokal an Festigkeit verliert. Das bedeutet, dass die Schweißnaht beim Umformen oder Tiefziehen reißt. An der Materialprüfungsanstalt (MPA) der Universität Stuttgart wurde nun ein Verfahren entwickelt, dass die Umformbarkeit von Taylor Welded Blanks (TWB) aus Aluminium erheblich verbessert. Das in der Abteilung Fügetechnik und Additive Fertigung unter Leitung von Martin Werz entwickelte Verfahren integriert eine Wärmebehandlung in den Fertigungsprozess.
Der Clou ist hierbei, dass die neu entwickelte Wärmebehandlungsstrategie bereits den Schweißprozess als lokales Lösungsglühen in den Prozessablauf mit einbezieht. Durch eine gezielt getaktete Wärmebehandlung direkt nach dem Schweißen ermöglicht das neue Verfahren einen bisher unerreichten Umformgrad und damit eine prozesssichere Integration von Tailor Welded Blanks aus Aluminium. Ein weiterer Vorteil ist der, dass das neue Verfahren auch auf hybride Tailor Welded Blanks aus Aluminium und Stahl angewendet werden kann. Durch Einsparung des Prozessschrittes Lösungsglühen können überdies sowohl der Energieeinsatz als auch die Fertigungskosten erheblich reduziert werden.
Das Verfahren besteht aus zwei Schritten, die problemlos in den Fertigungsprozess integriert werden können. Im ersten Schritt wird das lokale Lösungsglühen während des Schweißprozesses bei der Herstellung der TWBs genutzt, um in einer anschließenden Niedertemperatur-Warmauslagerung lediglich die Festigkeit der Schweißnaht vor dem Kaltumformen gezielt zu erhöhen und damit eine Dehnungslokalisation zu vermeiden. Die zweite Warmauslagerung erfolgt nach der Umformung während des Lackeinbrennens und erhöht die Festigkeit des gesamten Bauteils inkl. Schweißnaht bis zum Erreichen der Gebrauchseigenschaften.
Das Verfahren erlaubt ganz neue Einsatzgebiete und den prozesssicheren Einsatz von Al-TWB sowie Al-Stahl-TWB. Einer der Erfinder, Martin Werz, ist Spezialist für das Fügen von unterschiedlichen Materialien insbesondere durch Rührreibschweißen. Werz hält in diesem Bereich mehr als zwanzig Patente. Das neue Verfahren der besseren Umformbarkeit ergänzt die zahlreichen Innovationen des Schweiß-Spezialisten Werz in der Blechbearbeitung um das wesentliche Element der besseren Umformmöglichkeiten. Die Eignung des Verfahrens ist bereits in Zugversuchen mit entsprechend behandelten Schweißnähten demonstriert worden. Die Erfindung wurde in Deutschland und den USA zum Patent angemeldet.
TLB / JOL