Geschmolzen, nicht gefräst
Fortschritte bei additiver Fertigung dank neuer Lasertechnik.
Wo gehobelt wird, fallen Späne. Und wo Metalle geformt werden, fliegen die Funken. Letzteres verändert sich jedenfalls nicht, wenn neue Produktionsmethoden Einzug halten in die Fabrikhallen der Welt. Nur der Maßstab, in dem es funkt, wird etwas kleiner. Denn statt heißer Rohmasse oder gehärteten Werkstoffen führt der Laser Regie. Und der schichtet Ebene um Ebene, Mikrometer um Mikrometer an Metall- oder Kunststoffpulver aufeinander und verschmilzt diese – bis zum fertigen Produkt.
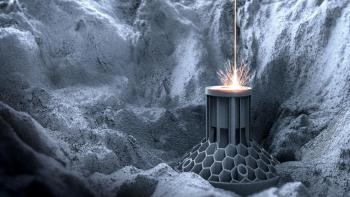
Das „additive manufacturing“ – umgangsprachlich gern als 3D-Druck bezeichnet – ist auf dem Weg, die Ideen der digitalen Welt greifbar zu machen. Christian Thönes, Vorstandsvorsitzender des Werkzeugmaschinenherstellers DMG Mori, sieht in diesem Verfahren den physikalischen Arm der Digitalisierung: „Additive manufacturing materialisiert die Ideen der Ingenieure und macht optimale Entwürfe aus der digitalen Welt in der realen Welt herstellbar.“ So müssten additiv gefertigte, komplexe Bauteile zum Beispiel nicht mehr aus achtzig Einzelteilen bestehen, sondern könnten als ein einziges, zusammenhängendes Stück produziert werden. Und die Form spielt dann auch keine Rolle mehr. Der Natur entlehnte Strukturen könnten den Weg weisen zu einer effektiveren Gestaltung von Kühlern, die beispielsweise Batteriepacks oder Brennstoffzellen umgeben und die trotz eines viel kleineren Bauvolumens den doppelten Wirkungsgrad traditionell gefertigter Komponenten bieten.
Geometrie und Physik setzen der konventionellen, „zerspanenden“ Fertigung mit Drehen oder Fräsen klare Grenzen. Zum Beispiel lässt sich eine Hohlwelle mit innenliegender Verrippung als reines Drehteil gar nicht – und mit der Kombination aus Drehen und Fräsen nur sehr eingeschränkt – herstellen. Dafür ist mindestens die Kombination mehrerer Einzelteile nötig. Additive Fertigungsmethoden erzeugen aus Metall- oder Kunststoffpulver und Laserenergie neue, hoch belastbare und ebenso komplexe Bauteile. Im Entwicklungszentrum Weissach erforschen Porsche-Ingenieure genau solche Verfahren, zum Beispiel um die Rotorwelle eines Elektromotors herzustellen.
Wie das im Detail funktioniert? Aktuell gibt es zwei Methoden: Beim Pulver-Düse-Verfahren wird Metallpulver über einen Gasstrom einer Düse zugeführt. Die Düse und ein Laserstrahl fokussieren denselben Punkt, an dem das Metallpulver vom Laser geschmolzen wird – dabei lässt sich der Produktionskopf aus Düse und Laser in bis zu fünf Achsen steuern. Beim Pulverbettverfahren schmilzt ein Laser das flächig ausgebrachte Metallpulver punktuell, wodurch das Bauteil in mehreren Schichten von zwanzig bis hundert Mikrometern Stärke in die Höhe wächst. So lassen sich nahezu alle erdenklichen Formen produzieren.
Die Vorteile von additiv gefertigten Werkzeugen: Dank exakt berechneter und umgesetzter Anforderungen sind sie dauerhaft belastbar und außerdem sortenrein im Recycling am Ende ihres Lebenszyklus. Kein Wunder also, dass auch DMG Mori-Chef Thönes von dieser neuen Technologie begeistert ist. Denn additiv gefertigte Teile bieten noch einen weiteren großen Vorteil: Sie ermöglichen die im Fahrzeugbau entscheidende Gewichtsersparnis. „Es kommt ja zunehmend darauf an, Bauteile leichter zu machen“, führt Thönes aus. „Das hilft den Automobilherstellern, den Treibstoffverbrauch zu reduzieren und den Kohlendioxid-Ausstoß zu senken.“
Allerdings weist er auf beide Seiten der Medaille hin: „Einerseits sind die Möglichkeiten nahezu grenzenlos. Wir können viel Gewicht einsparen, Funktionen optimal gestalten und absolut individuelle Bauteile realisieren. Andererseits stellt die Produktivität noch eine der großen Herausforderungen dar.“ Wenn es um die Produktionsgeschwindigkeit geht, haben klassische Pressen, Fräsen oder Gussverfahren nämlich derzeit noch die Nase vorn. Diese Erfahrung haben auch die Porsche-Ingenieure in Weissach gemacht: „Noch dauert es bis zu 13 Stunden, um solch eine Rotorwelle auszudrucken“, weiß Frank Ickinger, Vorentwicklung Motor.
Doch auch daran arbeiten die Ingenieure. Zum einen forschen sie mit Hochdruck daran, den additiven Aufbau von Werkstücken zu beschleunigen. Zum anderen optimieren die Entwickler permanent das Zusammenwirken von Teilen aus klassischer Produktion mit solchen, die mit den innovativen Methoden produziert werden. Und dank der neuen Technologie lassen sich unterschiedliche Materialien häufig leichter miteinander verbinden. „Eine Laserleistung, die fokussiert einige Tausend Grad Celsius erzeugt, kann zum Beispiel Edelstahl und Kunststoff miteinander verschmelzen“, erläutert Thönes.
Die enge Verzahnung innovativer Produktionstechniken mit moderner Informationstechnik ist für den Manager ein Baustein für die Fabrik der Zukunft. Die Art und Weise, wie Werkstücke und letztlich komplette Fahrzeuge künftig produziert werden, wird unter dem Schlagwort „Industrie 4.0“ zusammengefasst. Gemeint ist damit, dass die Kontrolle der Produktion durch Computer weit über die Ansteuerung von Fräsmaschinen oder Industrierobotern hinausgeht und letztlich alle Maschinen und Stationen der Produktion miteinander vernetzt. Davon profitieren nicht nur Fahrzeughersteller wie Porsche, auch den Kunden bietet die zukünftige vernetzte Produktion handfeste Vorteile. So können beispielsweise individuelle Kundenwünsche direkt in der Produktion erfüllt werden – und nicht erst in nachgelagerten Veredelungs- oder Manufakturprozessen. Zudem werden Änderungen von Sonderausstattungen, Farben, Felgen und Materialien durch den Kunden künftig bis unmittelbar vor Produktionsbeginn möglich sein.
Für Christian Thönes steht jedoch fest: „Bei allen Vorteilen des additive manufacturing ist klar: Traditionelle Fertigungsverfahren wie Drehen oder Fräsen bleiben auch in Zukunft bestehen.“ Genauigkeiten unter 0,1 Millimeter werden weiter von klassischen, hochpräzisen Werkzeugmaschinen gewährleistet.
Porsche AG / DE