Impedanz zerstörungsfrei messen
Neuer Messkopf bestimmt schwingungsbasiert den Zustand einer Struktur.
Ein vielversprechendes Verfahren in der zerstörungsfreien Prüfung struktureller Komponenten basiert auf der Messung der elektromechanischen Impedanz. Dafür wird normalerweise ein piezoelektrischer Wandler auf die Prüfstruktur geklebt, um die elektromechanische Kopplung herzustellen. Allerdings lässt sich der Wandler nach der Messung nur mit großem Aufwand entfernen. Dadurch besteht das Risiko, die Struktur zu beschädigen. Dies hat bisher die Anwendbarkeit des Verfahrens eingeschränkt, da der Messpunkt nicht flexibel geändert werden konnte und die Sensorik dauerhaft im Bauteil verbleiben musste. Daher hat ein Technologietransfer in die Industrie bisher nur für stationäre Anwendungen stattgefunden.
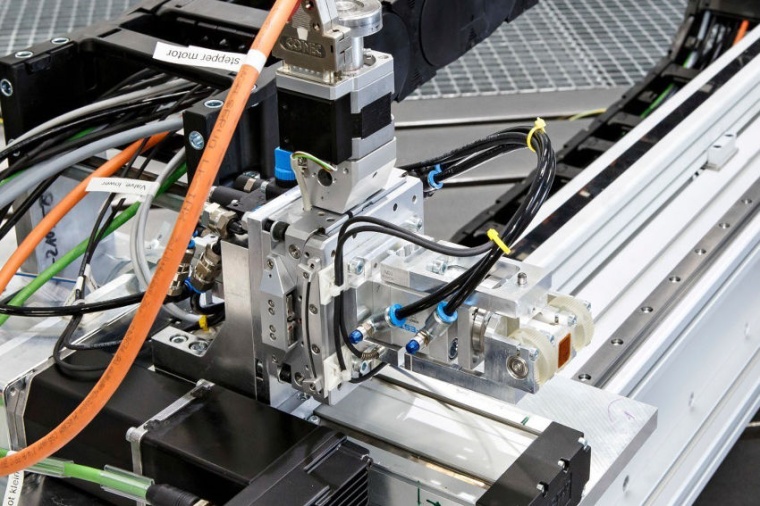
Kernelement des am Fraunhofer-Institut für Betriebsfestigkeit und Systemzuverlässigkeit LBF entwickelten Messkopfes ist ein piezoelektrischer Wandler mit einer Größe von 100 Quadratmillimeter. Einzigartig am Messkopf ist, dass er ohne zusätzliches Kopplungsmedium nur an die Prüfstruktur angedrückt wird und sich so auch wieder entfernen und an die nächste Messstelle bewegen lässt. Die Prüfstruktur wird somit nicht verändert, und es verbleiben auch keine Klebstoffrückstände auf ihrer Oberfläche. Der Messkopf ist imstande, simultan die Prüfstruktur anzuregen und die elektromechanische Impedanz zu messen.
Der Energieverbrauch des neuen Messkopfs liegt mit weniger als 500 Milliwatt deutlich unterhalb dem konventioneller Messverfahren, wo er eine Größenordnung höher liegt. „Auch im Hinblick auf die einstellbare, hohe Sensitivität ist der Messkopf konventionellen Verfahren überlegen und kann in der Identifikation von strukturellen Änderungen einen deutlichen Mehrwert für den Kunden aus der Prüf- und Messtechnik bis hin zu Endanwendern in der Automobil- und Luftfahrtindustrie generieren“, sagt Ye Ji Park, die das Projekt am Fraunhofer LBF betreut. Der Messkopf identifiziert strukturelle Änderungen, indem er Qualitätsabweichungen oder Materialfehler in der inline- oder offline-Fertigung detektiert. Zudem kann er Strukturfehler frühzeitig erkennen, um ein unerwartetes Materialversagen zu vermeiden.
Im Zuge einer vibrationsbasierten Messung zeigt der Messkopf im Vergleich zu akustischen oder optischen Systemen eine höhere Sensitivität für Strukturänderungen. Bei referenzbasierten Messungen erhöht der Messkopf die statistische Zuverlässigkeit und Entscheidungssicherheit. Darüber hinaus ermöglicht er es, strukturelle Änderungen über die Lebenszeit nachzuverfolgen.
Im Rahmen des durch die Europäische Kommission geförderten Luftfahrt-Forschungsprojekts Clean Sky 2 ist der Messkopf in ein automatisiertes Messsystem und in die Infrastruktur einer Produktionsanlage integriert worden. Derzeit ist auf diesem Wege eine Untersuchung von Strukturen bis zu einer Länge von rund acht Metern möglich. Mittelfristig ist geplant, die Signale des Messkopfs auch direkt für die Prozessoptimierung zu nutzen. Auf diese Weise trägt die Technologie nicht nur zur Überwachung, sondern auch zur Maximierung der Produktqualität bei.
Fh.-LBF / JOL