Kreislaufwirtschaft für Batterien
Projekt REWIND soll das Recycling von Lithium-Ionen-Batterien verbessern.
Ohne Lithium-Ionen-Batterien ist umweltfreundliche Mobilität und nachhaltige Energieversorgung kaum vorstellbar. Doch der steigende Bedarf an Batterien und die damit verbundenen Rohstoffe stellen uns vor große Herausforderungen. Mit dem Projekt „Rewind“ sollen wichtige Hindernisse auf dem Weg zu einer effizienten und ökologisch nachhaltigen Kreislaufwirtschaft überwunden werden. Es wird im Rahmen des BattFutur Programms des Bundesministeriums für Bildung und Forschung (BMBF) durchgeführt. Das Projektziel ist klar definiert: Die Recyclingfreundlichkeit von Batterien soll signifikant gesteigert werden, um die Ressourceneffizienz zu erhöhen und CO2-Emissionen zu reduzieren.
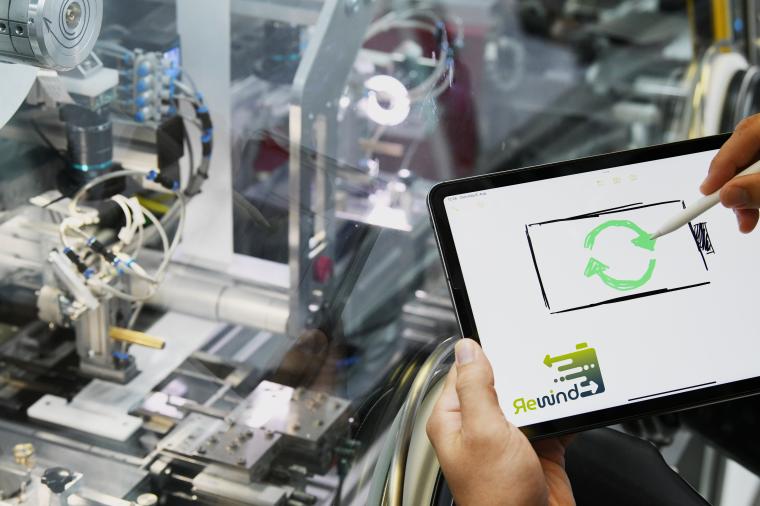
Ein zentrales Anliegen ist es, durch den Aufbau einer Nachwuchsgruppe am Fraunhofer FuE-Zentrum Elektromobilität (FZEB) des Fraunhofer-Instituts für Silicatforschung ISC, dem Fachkräftemangel entgegenzuwirken und wissenschaftlichen Nachwuchs für die Batterieforschung zu gewinnen. Dieses Vorhaben unterstützt das übergeordnete Ziel, ein „Kompetenzzentrum für direktes Recycling“ zu etablieren und damit die Grundlagen für zukünftige Innovationen zu legen. Das Projekt setzt damit neue Maßstäbe im Bereich des Batterierecyclings. Mit einem zirkulären Ansatz „ab initio“ zielt das Projekt darauf ab, eine Lithium-Ionen-Batterie (LIB) zu entwickeln, deren Prototyp nicht nur recyclingfreundlich ist, sondern deren Komponenten auch nahezu vollständig und strukturerhaltend zurückgewonnen werden können. Nach einem Regenerationsschritt können die Rezyklate dann direkt wieder in der Zellfertigung eingesetzt werden.
Trotz der Vorteile des direkten Recyclings – Ressourcenschonung und (potentiell) geringerer Produktionsaufwand durch den Verzicht des Hochtemperaturschritts während der Synthese der Aktivmaterialien – hat sich bisher noch kein entsprechendes Verfahren industriell durchgesetzt. Aktuell werden die Zellen deshalb meist mechanisch geschreddert und dann über hydrometallurgische Verfahren weiterverarbeitet – unter Gewinnung vieler Elemente, doch unter Verlust der Funktionsmaterialien. Das liegt vor allem am bislang geringen technologischen Reifegrad. So erschweren zum Beispiel Verunreinigungen durch mechanische vorgelagerte Prozesse die Verarbeitung, wobei besonders die notwendige Separation von Kathoden und Anoden eine technologische Hürde ist. Aufgrund der Vielfalt an LIB-Zellformaten und den unterschiedlichen Zellchemien ist die Trennung von Anode und Kathode bisher kaum wirtschaftlich möglich, da die Batteriezellen nicht über eine Kennzeichnung der Inhaltsstoffe verfügen.
Auch hier setzt das Projekt an und will die Kennzeichnung voranbringen, zum Beispiel in Kooperation mit Karl Mandel von der Friedrich-Alexander-Universität Erlangen-Nürnberg durch den Einsatz von Markerpartikeln, die eine einfache und zuverlässige Identifikation der Inhaltsstoffe ermöglichen. Das Herzstück aber ist die Entwicklung einer LIB-Zelle mit speziell gestalteten, recyclinggerechten Elektroden und Zelldesigns. So können Kathoden- und Anodenaktivmaterial sowie Leitruß und Zellgehäuse durch teils automatisierte wasserbasierte und energieeffiziente Prozesse regeneriert und direkt in neuen Batterien eingesetzt werden. Im Gegensatz zu herkömmlichen Recyclingmethoden wie pyrometallurgischen und hydrometallurgischen Verfahren bietet das direkte Recycling signifikante Vorteile, insbesondere bei der Rückgewinnung von funktionalen, aber weniger wertvollen Kathodenaktivmaterialien wie Lithiumeisenphosphat (LFP) und den Anodenmaterialien wie Graphit.
Angesichts der wachsenden Nachfrage nach LFP und dessen Bedeutung in der Batterietechnologie konzentriert sich das Projekt auf dieses Material. Zusätzlich wird das Konzept auf Natrium-Ionen-Batterien (NIB) übertragen, um die Anwendungsmöglichkeiten der entwickelten Technologien zu erweitern. Die Materialkosten für NIB sind im Vergleich zu LIB geringer. Aber es bestehen noch ungelöste technologische Herausforderungen wie eine geringere Energiedichte – und damit automatisch mehr Platzbedarf und Gewicht für die gleiche Batteriekapazität.
Das Fundament für „Rewind“ wurde durch eine Reihe öffentlicher Projekte wie AutoKlass, IDcycLIB, AdRecBat, NaKlar und ReUse gelegt, die maßgeblich vom Fraunhofer ISC initiiert und geleitet wurden. „Diese Projekte haben nicht nur wertvolles Wissen und eine robuste Infrastruktur geschaffen, sondern auch den Weg geebnet für eine effiziente Arbeit im Rewind-Projekt“, so Andreas Flegler, Leiter des Fraunhofer FuE-Zentrums Elektromobilität. Mit dem Projekt bietet sich die große Chance, den Kreislauf des direkten Recyclings zu schließen, ein tiefgreifendes Verständnis für den Gesamtprozess zu entwickeln und innovative Prozessschritte zu erarbeiten. Das Projekt soll in den Aufbau eines Kompetenzzentrums für direktes Recycling münden. Dieses soll eine Plattform für interessierte Industrieunternehmen wie Anlagenbauer, OEM oder Materialhersteller sein.
Fh.-ISC / JOL