Mit Volldampf ins Batteriezeitalter
Digitalisierung der gesamten Produktion sorgt für leistungsfähige und umweltschonende Batteriezellen.
Smartphone, Gabelstapler, Elektroauto – effektive Energiespeicher sind unerlässlich, um von fossilen Energieträgern auf sauberen Strom umsteigen zu können. Das Stuttgarter Fraunhofer-Institut für Produktionstechnik und Automatisierung IPA hat nun zusammen mit Partnern ein Projekt gestartet, das die Produktion von Batteriezellen kostengünstiger machen und deren Qualität verbessern soll.
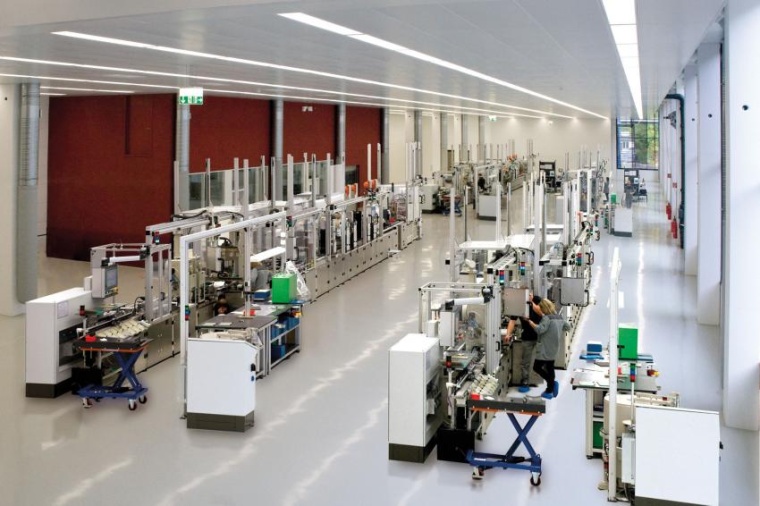
Das Ziel ist eine vollautomatische Produktion, die nicht nur fehlerhafte Werkstücke erkennt, sondern auch die Ursache dafür – und ohne Eingriff eines Menschen unverzüglich gegensteuert. Das ist nur möglich, wenn die gesamte Prozesskette digitalisiert ist und Sensoren zahllose Daten sammeln. In dieser Zukunftsfabrik wird alles erfasst: von den Einstellungen aller Maschinen über die Dicke der aufgetragenen Beschichtung bis zu Raumtemperatur und Luftfeuchtigkeit. Um im Datendschungel sinnvolle Zusammenhänge zu finden, braucht man künstliche Intelligenz. Sie ermittelt, bei welchen Einstellungen und Parametern mit welchem Ergebnis zu rechnen ist.
DigiBattPro4.0 steht für digitalisierte Batteriezellenproduktion mit Industrie-4.0-Technologien. Das Ziel des Projekts lässt sich freilich nicht im Labor erreichen. Für belastbare Ergebnisse braucht es eine reale Fertigung mit hohen Stückzahlen. Das ermöglicht der baden-württembergische Batteriekonzern Varta, der täglich zehntausende Batterien produziert. Hier werden die Fraunhofer-Experten zunächst alle Maschinen vernetzen und ein Computermodell erstellen. Der gesamte Produktionsprozess läuft dann nicht nur real ab, sondern auch virtuell. Das Modell soll zeigen, wie die Prozessgrößen die Produkteigenschaften beeinflussen, wo sich also Verbesserungen erreichen lassen – die Vorstufe zur selbstregelnden Fabrikation.
Was in der Bestandsproduktionslinie gelingt, soll im nächsten Schritt auf Lithium-Ionen-Batterien übertragen werden, wie sie etwa in Elektroautos stecken. Die Standardzellen sind zylinderförmig und messen 70 Millimeter in der Höhe und 21 Millimeter im Durchmesser. Experten sprechen vom 21700-Format. Das Projekt soll am Ende seiner Laufzeit die Voraussetzungen schaffen, um solche Zellen vollautomatisch mit Hilfe selbstregelnder störungsfreier Prozesse zu fertigen und damit Durchlaufzeiten zu verkürzen und Ausschuss zu reduzieren.
Die Zellen sollen auch durch neue Materialien leistungsfähiger und der Herstellungsprozess umweltschonender werden: Ein wässriges Kathodenmaterial ersetzt das umweltschädliche Lösungsmittel, außerdem erhöht ein angereicherter Nickelanteil die Energiedichte.
Die Verknüpfung von Digitalisierung und Materialentwicklung, an der neben dem Fraunhofer-Institut und Varta auch das Zentrum für Sonnenenergie und Wasserstoff-Forschung Baden-Württemberg ZSW beteiligt ist, gewährleistet rasche Ergebnisse. Das Projekt ist am 1. März angelaufen und soll vier Jahre laufen. „Langfristig werden die entwickelten Digitalisierungslösungen die Wirtschaftlichkeit der Batteriezellen¬produktion fördern und den Produktionsstandort Deutschland sichern“, ist IPA-Institutsleiter Alexander Sauer überzeugt.
Fh.-IPA / DE