Simulierte Schwingungen
Digitaler Zwilling erlaubt Vorhersage von Bauteilschwingungen bei der Fräsbearbeitung.
Bauteilschwingungen, die bei vielen Fertigungsverfahren entstehen, führen häufig dazu, dass die Oberfläche des Werkstücks beschädigt wird. Darüber hinaus sind sie ein Grund für erhöhten Werkzeugverschleiß. Das Fraunhofer-Institut für Produktionstechnologie IPT in Aachen hat erstmals gemeinsam mit Industriepartnern einen digitalen Zwilling entwickelt, mit dem sich Bauteilschwingungen bei der Fräsbearbeitung vorhersagen lassen. Mithilfe des digitalen Zwillings können bereits während der Prozessplanung optimale Prozessparameter ausgewählt und für eine ressourcenschonendere und kosteneffizientere Produktion verwendet werden.
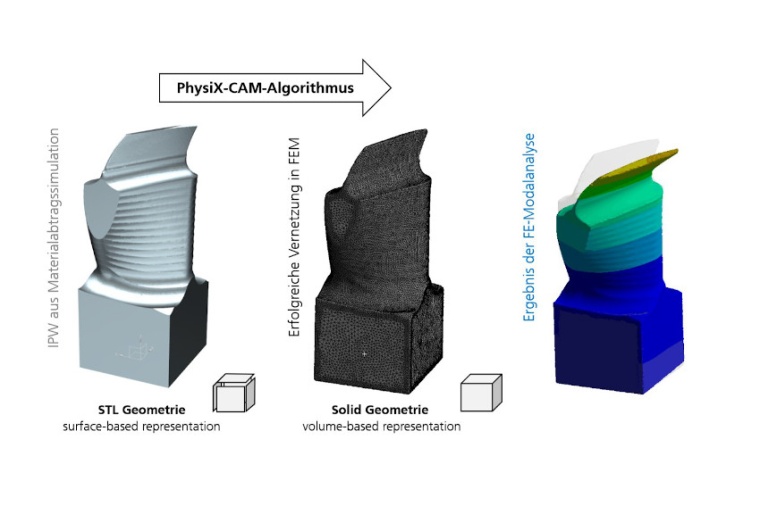
Bei der Fräsbearbeitung entstehen durch den charakteristischen unterbrochenen Schnitt sowohl am Bauteil als auch am Fräswerkzeug Schwingungen. Diese führen häufig dazu, dass die Oberfläche des Werkstücks beschädigt wird. In der Folge müssen die Bauteile zeit- und kostenintensiv nachbearbeitet werden. Hinzu kommt der hohe Werkzeugverschleiß, den die Prozessschwingungen verursachen. Dünnwandige Werkstücke, wie sie in der Luftfahrt oder auch in Leichtbau-Anwendungen vorkommen, haben ein besonders komplexes Schwingungsverhalten, das durch die Werkzeugposition und die eingesetzte Zerspankraft beeinflusst wird. Gängige Simulationen zur Materialzerspanung bilden zwar einzelne Zwischenzustände des Werkstücks während der Zerspanung ab. Um diese Modelle zur Analyse der dynamischen Schwingungseigenschaften nutzen zu können, müssen sie aber mit unverhältnismäßig hohem Aufwand manuell bearbeitet werden.
Ein Team des Fraunhofer IPT entwickelte im Forschungsprojekt „PhysiX-CAM“ erstmals einen digitalen Zwilling zur Vorhersage des Schwingungsverhaltens von Bauteilen am Beispiel einer Blade Integrated Disk (Blisk). Mithilfe des digitalen Zwillings gelang es den Forschenden, die Prozessparameter des Fräsprozesses so einzustellen, dass die Schwingungen auf ein Minimum reduziert werden. So ließen sich neue Prozessstrategien für die Fräsbearbeitung ableiten, die es ermöglichen, die Spindeldrehzahl während der Fertigung kontinuierlich und abhängig von der Werkzeugposition anzupassen und damit die Oberflächenqualität des Werkstücks deutlich zu verbessern.
Im ersten Projektabschnitt untersuchten sie mehrere Ansätze zur Modellierung der veränderlichen Werkstückgeometrie. Mit der Multi-Dexel-Modellierung, einer Methode zur geometrischen Modellierung und physikalischen Simulation, fand das Team eine Lösung, die eine hohe Genauigkeit bei vergleichsweise geringem Rechenaufwand bietet. Damit eignet sich die Methode besonders gut, um Modelle von Zwischengeometrien des Werkstücks, die In-Process-Workpieces (IPWs), zu erzeugen. Eine Schwäche der Multi-Dexel-Modellierung ist jedoch, dass sich mit ihr nur Oberflächen- und keine kompletten Volumenkörper modellieren lassen. Für Finite-Elemente-Simulationen zur Vorhersage des Werkstück-Schwingungsverhaltens brauchte das Aachener Team aber ein solches Volumenkörpermodell. Die Forschenden erweiterten deshalb mit viel Aufwand die Multi-Dexel-Modellierung und programmierten zahlreiche neue Funktionalitäten.
Nachdem sie erfolgreich die FE-Simulationen durchgeführt hatten, koppelten die Forscher diese Simulation mit der CAM-Software. Auf diese Weise schuf das Team eine voll automatisierte CAx-Software zur Ermittlung und Simulation der veränderlichen, dynamischen Werkstückeigenschaften. Darüber hinaus entwickelten sie auf Basis der Simulationen ein Stabilitätsdiagramm, mithilfe dessen sie, abhängig von Spindeldrehzahlen und Werkzeugpositionen, vorteilhafte und unvorteilhafte Bearbeitungsparameter für die Fräsbearbeitung identifizierten. Im nächsten Schritt testeten sie die Parameter in zahlreichen praktischen Zerspanuntersuchungen: Die in den praktischen Tests gemessenen Schwingungen stimmten nahezu vollständig mit den vorhergesagten überein. Aus den gewonnenen Erkenntnissen leiteten die Forscher im letzten Projektabschnitt neue Prozessstrategien für die Fräsbearbeitung ab, bei denen die Spindeldrehzahl während der Fertigung kontinuierlich und abhängig von der Werkzeugposition angepasst wird. Dies minimiert die Bauteilschwingungen.
Die entwickelte „PhysiX-CAM“-Technologie – der digitale Zwilling zur Schwingungsvorhersage – soll nach den erfolgreichen Versuchen zukünftig auch auf andere Fertigungsverfahren wie dem Drehen übertragen werden. Das Team des Fraunhofer IPT plant darüber hinaus, die Erfahrungen aus dem Forschungsprojekt auch für eine optimierte Nachbearbeitung additiv gefertigter Bauteile einzusetzen.
Fh.-IPT / JOL