Starker Schutz vor Wasserstoff
Neuartige Beschichtung schützt vor störender Versprödung.
Wasserstoff gilt als Hoffnungsträger der Energiewende. Noch aber sind einige Hürden zu überwinden, ehe der Wasserstoff in großem Stil zum Einsatz kommen kann. Eine Herausforderung besteht darin, dass atomarer Wasserstoff Metalle verspröden lässt. Das kann dazu führen, dass Bauteile versagen. Atomarer Wasserstoff sammelt sich ausgerechnet an jenen Stellen im Bauteil an, die besonders beansprucht sind, etwa an Schweißnähten oder in Bereichen, die unter Spannung stehen. Insbesondere bei Bauteilen, die hohen Betriebstemperaturen ausgesetzt sind, kann die Wasserstoffversprödung zum Problem werden. Der Physiker Lukas Gröner hat nun am Fraunhofer-Institut für Werkstoffmechanik IWM, MikroTribologie Centrum µTC, und am Institut für Mikrosystemtechnik der Universität Freiburg spezielle Beschichtungen für Bauteile aus Stahl entwickelt und getestet, die das Eindringen von atomarem Wasserstoff nahezu unterbinden.
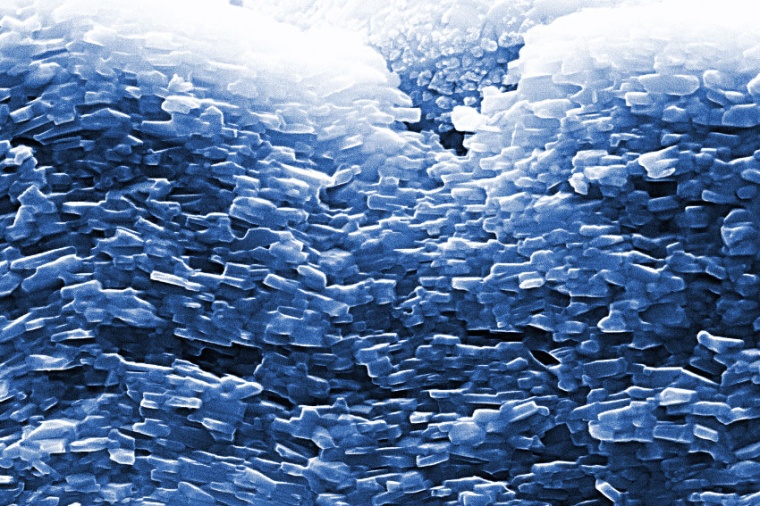
Dabei handelt es sich um MAX-Phasen-Materialien, an denen international seit mehr als zehn Jahren geforscht wird. „MAX-Phasen haben verblüffende Eigenschaften, weil sie Merkmale von Keramiken und Metallen vereinen“, so Lukas Gröner. MAX-Phasen sind, wie Keramiken, unempfindlich gegen Angriff durch Sauerstoff und sehr hitzebeständig. Zugleich sind sie elektrisch leitend wie Metalle. Und anders als reine Keramiken sind sie nicht spröde, weshalb sie nicht zerbrechen. Gröner ist es nun gelungen, dünne MAX-Phasen-Beschichtungen zu erzeugen, die den Stahl sehr gut vor Korrosion und Versprödung durch Wasserstoff schützen.
In einer Vakuumkammer schied er dazu zunächst sehr präzise abwechselnde Lagen aus Alumniniumnitrid und Titan auf einer Stahloberfläche ab mithilfe physikalischer Gasphasenabscheidung. Anschließend wurde dieser nur etwa drei Mikrometer dicke Sandwichaufbau erhitzt, wobei sich eine sehr dünne MAX-Phasen-Schicht aus Titan, Aluminium und Stickstoff bildete. Die Herausforderung bestand darin, das Abscheiden von Titan und Aluminiumnitrid so zu steuern, dass sich beim anschließenden Erhitzen parallele Ti2AlN-Plättchen ausbildeten. Das hat geklappt: „Die Plättchen liegen wie Ziegel in einem Mauerwerk dicht an dicht aufeinander“, sagt Gröner.
In seiner Promotion untersuchte Gröner auch, wie sich die MAX-Phasen-Beschichtung verhält, wenn sie stark erhitzt wird – so wie es künftig in Gasturbinen oder Brennstoffzellen der Fall sein könnte. Um übliche Betriebsbeanspruchungen nachzustellen, erwärmte er das Material auf 700 Grad und ließ es bis zu 1000 Stunden im Ofen. Dabei entstand an der Oberseite der Beschichtung eine dünne Lage aus einem speziellen Aluminium-Oxid – dem α-Al2O3. Wie sich im weiteren Verlauf der Untersuchungen zeigte, verstärkt dieser dünne Aluminium-Oxid-Belag die Barrierewirkung der Schutzschicht gegenüber Wasserstoff ganz erheblich.
Um zu prüfen, wie gut die MAX-Phasen-Schicht das Eindringen von Wasserstoff ins Metall verhindert, entwickelte Gröner zunächst einen Prüfstand für blechförmige Proben neu. In diesem Versuchsstand verglich er unbeschichtete Stähle mit MAX-Phasen-beschichteten Stählen. Damit ließ sich das Eindringen des Wasserstoffs genau quantifizieren und der Permeationsreduktionsfaktor (PRF) als Maß für die Barrierewirkung bestimmen. Die Ergebnisse lassen aufhorchen: Stähle mit einer MAX-Phasen-Schicht, die nicht erhitzt wurden, hielten den Wasserstoff immerhin 50-mal besser zurück als unbehandelte Stähle. Besonders eindrucksvoll aber waren die Ergebnisse für die beschichteten Stähle, die erhitzt worden waren und eine α-Al2O3-Schicht gebildet hatten. Diese hielten den Wasserstoff rund 3500-mal stärker zurück als der unbehandelte Stahl. „Das sind Werte, die den Anforderungen der Industrie absolut genügen“, sagt Gröner.
Wie gut die MAX-Phasen-Schichten in der Anwendung funktionieren, testet Gröner derzeit in Zusammenarbeit mit Kooperationspartnern wie dem Forschungszentrum Jülich – beispielsweise an Hochtemperaturbrennstoffzellen, die mit Betriebstemperaturen von rund 600 Grad Celsius arbeiten. Gröner: „Die MAX-Phasen-Beschichtungen sind für solche Anwendungen ideal, weil sie die metallischen Bauteile vor Hitze schützen und zugleich den elektrischen Strom ableiten können, der im Inneren der Brennstoffzelle entsteht.“ Auch für Gasturbinen sei die Beschichtung geeignet. Denn dem Erdgas soll künftig mehr und mehr regenerativ erzeugter Wasserstoff beigemischt werden, was dazu führt, dass das Gas mit höherer Temperatur verbrennt. Mehr Wasserstoff und höhere Temperaturen erhöhen aber das Risiko der Wasserstoffversprödung, weshalb eine Bauteil-Beschichtung mit α-Al2O3 hier sehr vorteilhaft sein kann. Ob das neue Beschichtungsverfahren künftig von der Industrie als Dienstleitung angeboten wird oder in anderer Form den Weg in den Markt findet, kann Gröner derzeit noch nicht sagen. Auch müssen die einzelnen Beschichtungs-Prozessschritte noch optimiert werden.
Fh.-IWM / JOL
Weitere Infos
- Originalveröffentlichung
L. Gröner et al.: Investigations of the Deuterium Permeability of As-Deposited and Oxidized Ti2AlN Coatings, Materials 13, 2085 (2020); DOI: 10.3390/ma13092085 - Tribologie, Fraunhofer-Institut für Werkstoffmechanik IWM, Freiburg