Windenergie: 1500 Sensoren für das Rotorblatt der Zukunft
Sensorik erlaubt erstmalig Untersuchung des Schwingungs- und Belastungsverhaltens sowie die Aerodynamik und Statik im laufenden Betrieb.
Rotorblätter gehören zu den Kernkomponenten einer Windenergieanlage. Sie sind bis zu siebzig Meter lang und wiegen zwischen 15 und 20 Tonnen. Um Windenergieanlagen in Zukunft effizienter zu betreiben und auch Standorte nutzen zu können, die weniger windintensiv sind, braucht es noch größere und gleichzeitig leichtere Blätter. Wie sich das realisieren lässt und welche technischen Herausforderungen damit verbunden sind, untersucht das Deutsche Zentrum für Luft- und Raumfahrt mit Partnern aus Forschung und Industrie.
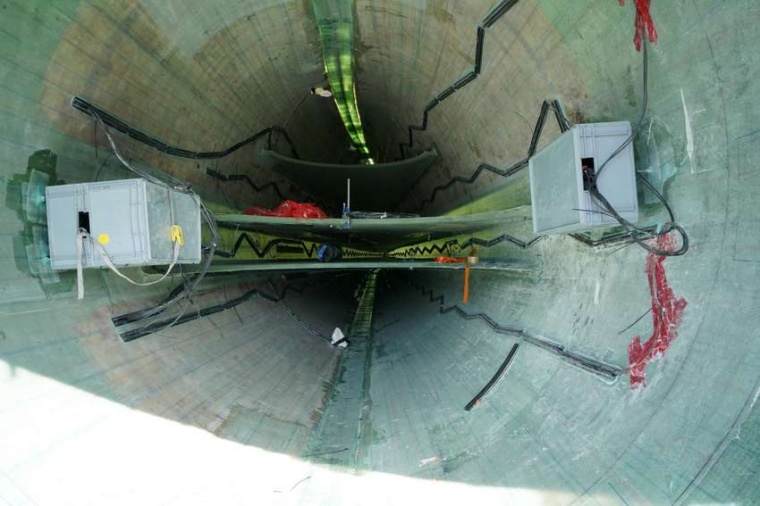
Der im Aufbau befindliche Forschungspark Windenergie WiValdi des DLR in Krummendeich bietet dazu eine einmalige Gelegenheit: Über mehrere Wochen im März und April 2022 haben Wissenschaftler der DLR-Institute für Aeroelastik sowie für Faserverbundleichtbau und Adaptronik mit der zum Zentrum für Windenergieforschung ForWind gehörenden Leibniz-Universität Hannover die Produktion von sechs Rotorblättern für die beiden Windenergieanlagen des Forschungsparks begleitet. Im portugiesischen Werk des Industriepartners Enercon rüstete das Team die Rotorblätter mit etwa 1500 Sensoren aus. Von der Blattspitze bis zur Blattwurzel steht nun modernste Messtechnik bereit. Diese ermöglicht es erstmals, das Schwingungs- und Belastungsverhalten sowie die Aerodynamik und Statik einer Windenergieanlage im Realmaßstab und Praxisbetrieb umfassend wissenschaftlich zu untersuchen.
„Wenn man große und leichte Blätter hat, werden diese sehr elastisch und flexibel. Sie biegen sich unter Windlast durch. Damit sind neue technische Herausforderungen verbunden, die man sich genau anschauen muss“, erklärt Yves Govers vom DLR-Institut für Aeroelastik und Leiter des Arbeitspakets zur Instrumentierung. Die Rotorblätter der beiden Windenergieanlagen des Forschungsparks sind 57 Meter lang und können sich mehrere Meter durchbiegen.
„Die Sensoren kann man sich wie das menschliche Nervensystem vorstellen. Sie sammeln Informationen, überwachen und geben Hinweise, wo ein Problem auftauchen könnte“, so Govers. Im Inneren der Rotorblätter sind elektrische und optische Sensoren verbaut. Sie messen zum Beispiel die Beschleunigung an unterschiedlichen Stellen der Blätter und ermöglichen so Aussagen über das Schwingungsverhalten. Faseroptische Dehnungssensoren, die mit Lasertechnologie arbeiten, zeichnen die Belastungen auf, die auf das Material wirken. Ein Netzwerk aus piezoelektrischen Wandlern empfängt und sendet Ultraschallsignale und kann entstehende Schäden im Rotorblatt direkt erkennen. Weitere Kameras im Umfeld der Windenergieanlagen schauen sich die Rotorblätter von außen an. Als Referenz für deren Messungen ist auf mehreren Abschnitten der Blätter ein Muster aus Punkten lackiert.
Werden die Blätter immer länger und die Anlagen dadurch größer, entstehen neue Effekte: Zum Beispiel können sich Schwingungen der Rotorblätter gegenseitig verstärken und die Stabilität der Anlage beeinflussen. „Das Schwingungsverhalten und damit auch die Materialbelastung konnten im Betrieb bisher kaum erfasst werden. Hier werden wir mit unserer umfassenden Sensorik wertvolle Daten sammeln und die Simulationen weiter verbessern können. Dieses Wissen hilft Forschung und Industrie dabei, genauere Vorhersagen zu treffen sowie noch leichter und stabiler zu bauen“, sagt Govers. Schon heute vereinen Rotorblätter Leichtbau mit Stabilität. Sie bestehen aus zwei zusammengeklebten Schalen, die innen weitgehend hohl und mit Stegen verbunden sind. Zum Einsatz kommen Sandwich-Materialien: Sie haben oben und unten eine Decklage aus mit Glasfasern verstärkten Hightech-Kunststoffen, dazwischen befindet sich Kunststoffschaum oder sehr leichtes Balsaholz.
Unter Belastung verbiegt sich das Rotorblatt nicht nur, sondern verdreht sich zusätzlich. Die Sensoren im Inneren der Blätter zeichnen auch das auf. Diese Daten können helfen, neue Ansätze für die Regelung von Windenergieanlagen zu entwickeln, um sie effizienter und länger zu betreiben. Das DLR arbeitet dazu an Konzepten für eine lastadaptive Regelung von Anlagen: Kommt eine Böe auf, drehen spezielle Motoren an der Blattwurzel das Rotorblatt aus dem Wind. Sie verkleinern also den Winkel, in dem der Wind auf das Blatt trifft, und verringern die Belastung. In Verbindung mit Sensoren im Umfeld der Windenergieanlagen soll es so möglich werden, sehr kurzfristig und flexibel auf die lokalen Wetterbedingungen vor Ort zu reagieren.
Auch zwei hintereinanderstehende Windenergieanlagen – wie im Forschungspark des DLR – sind eine Herausforderung für die Regelungstechnik. Denn die zweite Anlage steht im Nachlauf der ersten. Das heißt, sie bekommt die verwirbelte Luft der ersten Anlage ab. Deshalb wollen die Forscher herausfinden, wie die zweite Anlage gesteuert werden muss, damit sie trotzdem möglichst viel Strom produziert und materialschonend betrieben werden kann. Auch hier setzen die Wissenschaftler auf die große Menge an Daten aus den vielzähligen Sensoren. Die Nachfrage nach solchen neuen Regelungskonzepten ist groß. Denn schon heute stehen in Windparks die teilweise über hundert Anlagen so dicht zusammen, dass sie sich alle gegenseitig beeinflussen.
Nach ihrer Schiffsreise von Portugal nach Deutschland Mitte Mai 2022 haben die sechs Rotorblätter noch eine weitere Station vor sich. Bevor sie im Forschungspark in Krummendeich montiert werden, machen sie für zwei Monate einen Zwischenstopp in Bremerhaven. Am Fraunhofer-Institut für Windenergiesysteme werden sie intensiven Tests an Prüfständen unterzogen. Dazu hängt das Team die Rotorblätter mit Gummiseilen an einen Kran und versetzt sie in Schwingung. Damit sollen vor allem die vielen Sensoren eingerichtet und getestet werden. Bei einem zweiten großen Test montieren die Forscher die Blätter an einen Prüfstand und ziehen an ihnen, um so Statik, Deformation und innere Belastung zu testen. Nach Abschluss dieser Versuche ist die Montage der Hightech-Rotorblätter im Herbst 2022 geplant.
DLR / RK
Weitere Infos
- Institut für Aeroelastik, Strukturdynamik und Systemidentifikation, Deutsches Zentrum für Luft- und Raumfahrt, Göttingen
- Institut für Faserverbundleichtbau und Adaptronik, Deutsches Zentrum für Luft- und Raumfahrt, Braunschweig