Zähne aus dem 3D-Drucker
Additive Fertigung drängt mit ersten Prototypen in die Medizintechnik.
Es geht um Hightech-Zahnersatz, um Prothesen, die Entzündungsreaktionen im Körper eigenständig erkennen oder individuell angepasste Sitze für Rollstühle. Ein deutsch-polnisches Leistungszentrum der Fraunhofer-Gesellschaft erforscht neue Technologien für den Einsatz von 3D-Druckverfahren, der additiven Fertigung, in der Medizintechnik. Für die Fraunhofer-Gesellschaft ist es eines von zwei im März gestarteten internationalen Leistungszentren, die sich explizit der grenzübergreifenden Zusammenarbeit widmen. Beteiligt am Zentrum „Additive Technologien für Medizin und Gesundheit“ (ATeM) sind auf deutscher Seite das Fraunhofer-Institut für Werkstoff- und Strahltechnik IWS in Dresden sowie das Fraunhofer-Institut für Werkzeugmaschinen und Umformtechnik IWU in Chemnitz. Sie kooperieren mit der Fakultät Maschinenbau und dem Center for Advanced Manufacturing Technologies (CAMT) der Technischen Universität Breslau.
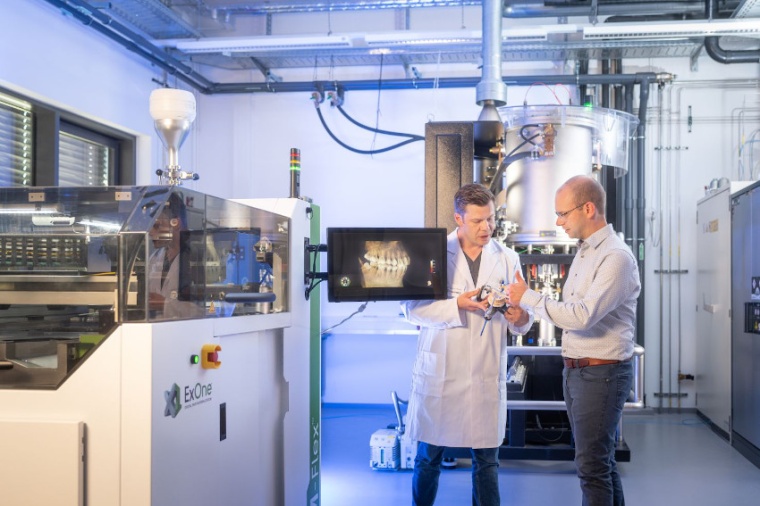
Der 3D-Druck erlaubt individuelle und auf den Patienten zugeschnittene Lösungen sowie die Integration neuer, verbesserter Eigenschaften und Funktionen in Bauteile. Dies ist meist nicht nur deutlich kostengünstiger als herkömmliche Verfahren, sondern erlaubt auch, neuartige Therapien und Behandlungsansätze bereitzustellen. Das Leistungszentrum ATeM möchte die additive Fertigung in den kommenden Jahren zum etablierten Standardwerkzeug in der Medizintechnik machen. Ende des Jahres wollen die Projektpartner bereits erste Demonstratoren vorstellen. In verschiedenen Einzelprojekten loten die Partner dafür neue Anwendungsfelder aus. Eines der Projekte beschäftigt sich mit den Chancen des 3D-Drucks in der Zahnmedizin. „Großes Potential liegt in der Nutzung innovativer Werkstoffe und der Integration zusätzlicher Funktionalitäten in den Zahnersatz, die den Tragekomfort für den Patienten erhöhen“, erklärt dazu Frank Brückner, Technologiefeldleiter Generieren und Drucken am Fraunhofer IWS. Die additive Fertigung könnte es gestatten, deutlich komplexere Implantate nach einem 3D-Scan des Mundraums sofort zu drucken und damit Wartezeiten zu verkürzen. Über additive Verfahren ließen sich beispielsweise auch Metall- und Kunststoffmaterialien für eine verbesserte Ästhetik miteinander kombinieren.
Ein weiteres Anwendungsszenario betrifft Funktionserweiterungen, wie etwa die direkte Integration von Sensoren in medizinische Komponenten. Empfindliche Sensoren in additiv hergestellten Knie- oder Hüftgelenken könnten Entzündungsreaktionen nach der Operation feststellen, indem sie auf höhere Temperaturen oder veränderte Biomarker reagieren. Ebenfalls gedruckt werden sollen in Zukunft Lab-on-a-Chip-Systeme, mit denen sich Organfunktionen und Abläufe im menschlichen Körper auf einem Chip darstellen lassen. Das kann beispielsweise beim Testen von Medikamenten zum Einsatz kommen.
Wie sich faserverstärkte 3D-Strukturen drucken lassen, erforschen derzeit Wissenschaftler in zwei Projekten unter der Leitung des Fraunhofer IWU. „Ein belastungsgerechtes Design eines Produkts, das dazu noch sehr leicht ist, erreichen wir mit dem Einsatz von Verstärkungsfasern, die wir direkt in die Kunststoffmatrix einbringen“, sagt Lothar Kroll, Wissenschaftlicher Direktor Leichtbau- und Textiltechnologien am Fraunhofer IWU. Damit ließen sich beispielsweise Schädelimplantate aus dem biokompatiblen thermoplastischen Kunststoff Polyetheretherketon (PEEK) drucken. Auch an individuell angepassten Sitzen für Rollstühle sowie hochfesten Orthesen arbeiten die Forschenden momentan.
Bereits seit 2008 existiert ein Fraunhofer-Project-Center, das vom Fraunhofer IWS und dem CAMT der TU Breslau betrieben wird. „Wir freuen uns, dass wir mit dem neuen Leistungszentrum nun die Synergieeffekte dieser erfolgreichen Zusammenarbeit weiter ausbauen können“, sagt Edward Chlebus, Dekan der Fakultät Maschinenbau der TU Wroclaw. Das in Deutschland von der Fraunhofer-Gesellschaft bereits langjährig erprobte Model der Leistungszentren richtet einen starken Fokus auf den Wissenstransfer und Industriekooperationen. Auch grenzübergreifend setzt es nun wichtige Impulse für die Stärkung der europäischen Wirtschaft. „Alle Partner sind Experten auf dem Gebiet der additiven Fertigung“, so Robin Willner, Wissenschaftler am Fraunhofer IWS und Koordinator der Geschäftsstelle des deutsch-polnischen Leitungszentrums. Die TU Breslau sei zudem noch sehr eng mit der dortigen Medizinischen Fakultät verbunden. „Zusammen haben wir nun einen guten Blick darauf, wo Bedarfe bestehen, wo bisher noch keine Lösungen gefunden wurden und additive Technologien im Medizin- und Gesundheitsbereich Mehrwerte schaffen könnten.“
Bereits Ende des dritten Quartals 2021 wollen die Beteiligten erste Demonstratoren zu den verschiedenen Projekten präsentieren. Das ist zügig möglich, weil die Partnereinrichtungen wichtige Grundlagen für die aktuelle Forschung in der Vergangenheit bereits in verschiedenen Vorstudien realisierten. Über Industriekooperationen oder mögliche Ausgründungen sollen die Ideen für neue Medizinprodukte und Therapien bereits in naher Zukunft den Patienten zugutekommen.
Fh.-IWS / JOL