Hitzeschilde für sparsame Flugzeuge
Keramikschichten auf Turbinenschaufeln können Triebwerkabgase verringern.
Damit Flugzeuge sparsamer, umweltfreundlicher und robuster werden, haben Forscher am Fraunhofer-
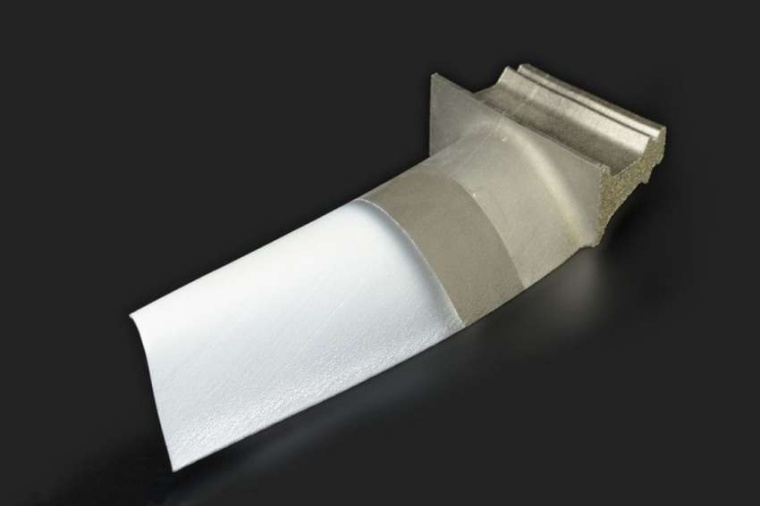
„Damit werden hochwertige und langlebige Schutzschichten selbst auf großen Bauteilen möglich – zu vergleichsweise niedrigen Kosten“, betont Barbosa. „Indem wir Suspensionen statt Pulver spritzen, können wir Werkstoffe mit sehr kleinen Partikeln einsetzen, die bisher nicht dafür geeignet waren. Wir schlagen hier eine Brücke zwischen den etablierten Beschichtungsverfahren, die alle ihre Vor- und Nachteile haben. In Zukunft lassen sich damit auch neuartige Werkstoffkompositionen verarbeiten.“ Um Wärmedämmschichten zu erzeugen, sind bisher vor allem zwei Technologiepfade üblich: Einige Unternehmen bearbeiten die Bauteile mit Elektronenstrahlverdampfern in Vakuumkammern. Dabei entstehen sehr hochwertige und langlebige Schichten. Aber dieses Verfahren ist teuer, insbesondere für die Beschichtung sehr großer Bauteile. Der zweite Technologiepfad ist das atmosphärische Plasmaspritzen. Dabei wird Pulver in einem Plasmastrahl geschmolzen und auf das Bauteil geschleudert. Das ist zwar relativ preiswert, weil es ohne Vakuumkammern auskommt. Aber die so erzeugten Schutzschichten sind wenig belastbar.
Mit dem „YSZ-Suspensionsspritzen“ haben die Forscher jetzt eine Alternative entwickelt. Die Körner in dem Pulver weisen einen Durchmesser von nur einem Mikrometer auf oder sind noch kleiner. Solche besonders feinen Pulver würden in klassischen Verarbeitungsverfahren sehr rasch verklumpen und die Maschinenschläuche verstopfen. Deshalb rühren die Ingenieure mit Wasser oder Alkohol eine Suspension an. Auf diese Weise werden die Partikel dann doch spritzbar. Dabei entsteht eine Abschirmschicht, die etwa fünfhundert Mikrometer dünn ist. Weil dafür kein Vakuum nötig ist, bleiben die Kosten überschaubar. Zudem lassen sich so auch große Flugzeug-
„Auch die Umwelt wird weniger belastet, weil der Treibstoff in den verbesserten Triebwerken effizienter verbrennt, was den Kraftstoffverbrauch reduziert und entsprechend weniger Schadstoffe ausstößt“, so Barbosa ein. Um einen weiteren Vorteil neuer Triebwerksbeschichtungen zu verstehen, lohnt sich eine Zeitreise ins Jahr 2010: Als damals der isländische Vulkan Eyjafjallajökull ausbrach, legte er den Flugverkehr in halb Europa lahm. Abgesehen von den Sichtproblemen durch die hochgeschleuderte Vulkanasche sorgten sich die Fluggesellschaften auch über mögliche Turbinenschäden. Denn diese Asche enthält, ähnlich wie der nicht minder schädliche Flugsand, Kalzium-
Eben gegen diese Schäden kann eine qualitativ hochwertige Zusatzschicht helfen, die nicht gleich wieder abplatzt. Auch darauf zielt das neue Suspensionsspritzverfahren. „Für diesen Anwendungsfall arbeiten wir mit dem DLR und der TU Dresden zusammen“, sagt Barbosa. „Wir wollen gemeinsam eine Opferschicht entwickeln, damit Asche und Sand nicht gleich die Turbinenschaufel selbst angreifen können. Die Flugzeuge sollen dadurch auch nach einem Vulkanausbruch noch sicher ihr Ziel erreichen.“
Auch in der Halbleiterbranche stößt das IWS-Verfahren auf großes Interesse. Denn in der Chipproduktion setzen die großen Mikroelektronikfabriken unter anderem Plasma-
Fh.-IWS / RK
Weitere Infos