Hybridleiter statt Keramik
Neues Laserverfahren für effiziente Leistungselektronik.
Am Fraunhofer-Institut für Lasertechnik ILT ist es in Zusammenarbeit mit Projektpartnern gelungen, ein neuartiges industrielles Fertigungsverfahren zu entwickeln. Es ermöglicht kostengünstige FR4-Leiterplattensubstrate jetzt auch in der Leistungselektronik, zum Beispiel in Elektromotoren, anzuwenden. Gegenüber dem Einsatz von konventioneller Leistungselektronik aus Keramik sind die Hybridleiterplatten nicht nur wesentlich vielseitiger einsetzbar, sondern auch bis zu zwanzigmal günstiger. Das könnte mittelfristig eine Marktlücke schließen und so einen wichtigen Beitrag zur Mobilität der Zukunft leisten.
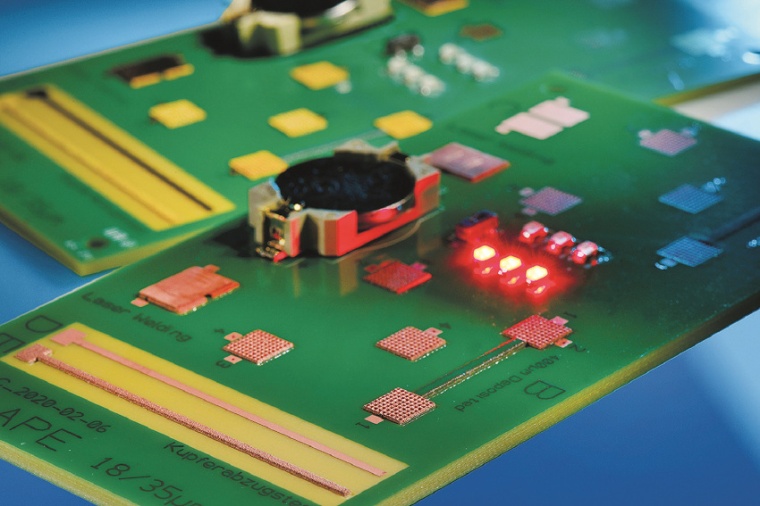
„Stellen Sie sich einen Kupferblock mit gleicher Fläche, aber unterschiedlicher Dicke im Querschnitt vor“, bricht Projektleiter Woo-Sik Chung aus der Gruppe Mikrofügen das Prinzip des neu entwickelten Fertigungsverfahren auf seine Essenz herunter. „Je dicker der Block, desto größer die Stromübertragung. Dort, wo am meisten Strom benötigt wird, verstärken wir die Leiterplatte. Dort, wo nur wenig Strom hindurchfließen muss, sparen wir Material ein.“ Mit standardisierten Herstellungsverfahren war es bislang sehr aufwändig, einzelne Bereiche gezielt so zu verdicken, dass eine geschweißte Verbindung angebracht werden kann. Im Projekt CLAPE nahmen sich Experten des Fraunhofer ILT, des Unternehmens ILFA und der französischen KMU Ouest Coating in den vergangenen drei Jahren dieser Herausforderung erfolgreich an.
„Bisher galt: man verwendet eine Leiterplatte mit dünner Metallisierung oder eine mit dicker. Entweder-oder. Je nach Einsatzzweck“, erklärt Chung. Ein Stromwandler, um Akkus in E-Autos zu laden beispielsweise benötigt zur Leistungsübertragung viel Strom innerhalb eines kurzen Zeitraums. Um ein Stromsignal an eine LED-Leuchte zu übertragen, bedarf es dagegen nur weniger Milliampere. „Unser neues Fertigungsverfahren ermöglicht es, beides auf nur einer Leiterplatte gleichzeitig zu realisieren: Signal- und Stromübertragung.“ Möglich machte dies die erfolgreiche Kombination zweier bewährter Prozesse. Dazu verwendeten die Forscher speziell angepasste Leiterplatten. Sie wurden per Kaltgassprühverfahren lokal nach konkretem Bedarf genau so verdickt, dass unterschiedlich starke Leiterbahnen ohne thermische Beschädigung per Laserstrahlmikroschweißen stoffschlüssig mit der Leiterplatte verschweißt werden konnten. Vorteil des Verfahrens: Die dabei entstandenen Hybridleiterplatten benötigen dank ihres spezifischen Aufbaus zur Signal- und Stromübertragung nicht nur weniger Platz, sondern verteilen die Energie auch wesentlich effizienter.
„Perspektivisch könnten unsere Hybridleiterplatten so mehrere Funktionen innerhalb eines Bauteils zusammenfassen“, sagt Woo-Sik Chung. „Setzt sich das Verfahren in der Praxis durch, könnte sowohl der Bauraum für die Leistungselektronik als auch das Gesamtgewicht von E-Autos signifikant reduziert werden, was sowohl in einer höheren Reichweite als auch einem langfristig geringeren CO2-Ausstoß münden würde.“ Auch in Anbetracht der Tatsache, dass die benötigten Ressourcen zur Herstellung von Chips für die Leistungselektronik knapp bemessen sind, ist das eine überaus wichtige Erkenntnis.
Dass mit der höheren Effizienz auch eine größere Wirtschaftlichkeit einhergeht, macht die Neuentwicklung für die Industrie besonders interessant. Vor allem, wenn man an die erst kürzlich weiter nach oben korrigierten deutschen Klimaziele denkt, nach denen bis 2030 65 Prozent CO2 eingespart und das Land bis 2045 klimaneutral werden soll. Statt weniger zentraler Stromversorger soll es dann ein dezentrales Netz vieler Energielieferanten geben. Solarzellen zum Beispiel, private Biogas- und Windkraftanlagen. Ein weiterer zentraler Strategiebaustein: die E-Mobilität. So könnten Batterien von E-Autos Energie künftig speichern oder bereitstellen.
„Wir haben das Projekt vor Kurzem erst abgeschlossen“, sagt Chung. „Die Technologie ist zwar noch nicht marktreif und bis zum praktischen Einsatz sind noch einige Anpassungen nötig. Wir konnten aber jetzt schon aufzeigen, dass es vielversprechende technologische Alternativen zum Status quo gibt.“ Das nächste Forschungsziel ist es nun, die Selektivität beim Kaltgassprühverfahren zu optimieren und die Kosten weiter zu reduzieren. „Hier haben wir noch Luft nach oben. Das zeigt uns aber auch, welch großes Potenzial in der Technologie liegt, sobald sie wirtschaftlich rentabel genutzt werden kann“, sagt Chung.
Fh.-ILT / JOL