Letztes Segment für den weltgrößten Teleskopspiegel gegossen
Wichtiges Modul für das Extremely Large Telescope in der Atacama-Wüste geht auf die Reise.
Das Extremely Large Telescope (ELT) der Europäischen Südsternwarte Eso, das in der chilenischen Atacama-Wüste gebaut wird, ist seiner Fertigstellung einen Schritt näher gekommen. Das deutsche Unternehmen Schott hat erfolgreich den Rohling für das letzte der 949 Segmente gegossen, die für den Hauptspiegel (M1) des Teleskops in Auftrag gegeben wurden. Mit einem Durchmesser von mehr als 39 Metern wird der M1 der mit Abstand größte Spiegel sein, der je für ein Teleskop hergestellt wurde.
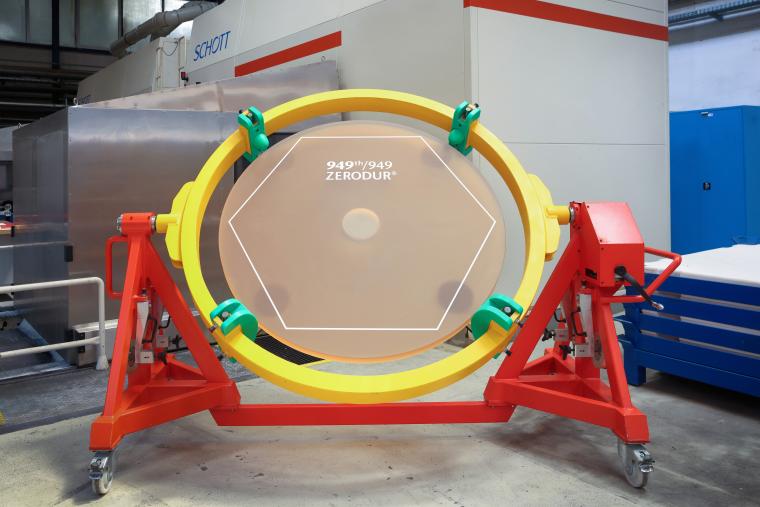
Aufgrund seiner Größe kann der M1 nicht aus einem einzigen Stück Glas gefertigt werden. Er besteht aus 798 sechseckigen Segmenten, die jeweils etwa fünf Zentimeter dick und anderthalb Meter breit sind und zusammen zehn Millionen Mal mehr Licht sammeln als das menschliche Auge. Weitere 133 Segmente wurden hergestellt, um die Wartung und Neubeschichtung der Segmente zu erleichtern, sobald das Teleskop in Betrieb ist. ESO hat außerdem achtzehn Ersatzsegmente beschafft, sodass die Gesamtzahl nun 949 beträgt. Die M1-Rohlinge, geformte Werkstücke, die später zu Spiegelsegmenten poliert werden, bestehen aus Zerodur, einer Glaskeramik mit geringer Ausdehnung, das für die extremen Temperaturbereiche am Standort des ELT in der Atacama-Wüste optimiert wurde. Schott hat auch die Rohlinge von drei weiteren ELT-Spiegeln – M2, M3 und M4 – in seinen Werken in Mainz hergestellt.
„Eso hat bei Schott mehr als nur Zerodur bestellt“, sagt Marc Cayrel, Leiter der ELT-Optomechanik. „In enger Zusammenarbeit wurde jeder einzelne Produktionsschritt optimiert und das Produkt so angepasst, dass es die sehr hohen Anforderungen des ELT erfüllt und oft sogar übertrifft. Die hervorragende Qualität der Rohlinge wurde während der Massenproduktion von mehr als 230 Tonnen dieses Hochleistungsmaterials beibehalten.“ Thomas Werner, Projektleiter bei Schott, sagt: „Unser gesamtes Team ist begeistert, dass wir den größten Einzelauftrag für Zerodur in der Geschichte unseres Unternehmens abschließen konnten. Für dieses Projekt haben wir die Serienproduktion von Hunderten von Zerodur-Spiegelsubstraten erfolgreich abgeschlossen, während wir normalerweise nur Einzelstücke herstellen.“
Nach dem Guss durchlaufen alle Segmente ein mehrstufiges, internationales Verfahren. Nach einer langsamen Abkühlungs- und Wärmebehandlungsphase wird die Oberfläche jedes Rohlings durch ultrapräzises Schleifen geformt. Anschließend werden die Rohlinge an das französische Unternehmen Safran Reosc geliefert, wo jeder Rohling in eine sechseckige Form geschnitten und auf einer optischen Fläche mit einer Genauigkeit von zehn Nanometern poliert wird. An der Arbeit an den M1-Segmentbaugruppen sind außerdem beteiligt: das niederländische Unternehmen VDL ETG Projects BV, das die Segmentstützen herstellt; das deutsch-französische FAMES-Konsortium, das die 4500 nanometergenauen Sensoren zur Überwachung der relativen Position jedes Segments entwickelt hat und deren Herstellung abschließt; das deutsche Unternehmen Physik Instrumente, das die 2500 Stellmotoren entwickelt hat, die das Segment nanometergenau positionieren können, und das dänische Unternehmen DSV, das für den Transport der Segmente nach Chile zuständig ist.
Nach dem Polieren und Zusammenbau wird jedes M1-Segment über den Ozean zur technischen Einrichtung des ELT am Paranal-Observatorium der ESO in der Atacama-Wüste transportiert – eine 10.000 Kilometer lange Reise, die bereits mehr als siebzig M1-Segmente hinter sich haben. Am Paranal, nur wenige Kilometer von der Baustelle des ELT entfernt, wird jedes Segment mit einer reflektierenden Silberschicht überzogen und anschließend sorgfältig gelagert, bis die Hauptstruktur des Teleskops bereit ist, sie aufzunehmen. Wenn es später in diesem Jahrzehnt in Betrieb genommen wird, wird das ELT das größte Auge am Himmel sein.
MPIA / JOL